Manutenção preventiva e calibração de equipamentos para garantir eficiência e durabilidade
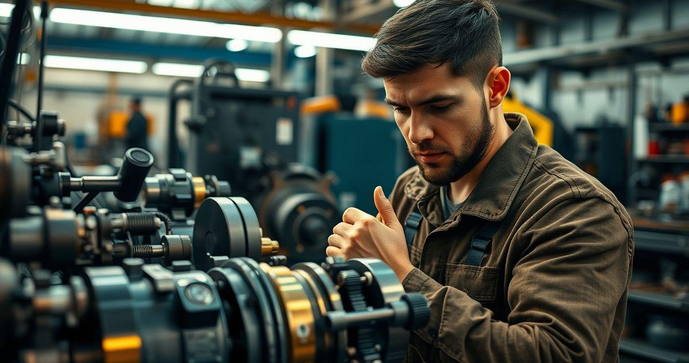
Por: Mauricio - 26 de Janeiro de 2025
A manutenção preventiva e calibração de equipamentos são práticas fundamentais para garantir o funcionamento eficiente e a longevidade dos dispositivos utilizados em diversas indústrias. Com a crescente dependência de tecnologia e maquinário, entender a importância dessas ações se torna essencial para evitar falhas e reduzir custos operacionais. Neste artigo, abordaremos os principais aspectos da manutenção preventiva e calibração, destacando suas vantagens e melhores práticas.
Importância da Manutenção Preventiva para Equipamentos
A manutenção preventiva é uma estratégia essencial para garantir a eficiência e a durabilidade dos equipamentos utilizados em diversos setores. Essa prática envolve a realização de inspeções regulares, ajustes e reparos programados, visando evitar falhas e prolongar a vida útil dos dispositivos. A seguir, discutiremos a importância da manutenção preventiva e como ela pode impactar positivamente a operação de uma empresa.
Um dos principais benefícios da manutenção preventiva é a redução de custos operacionais. Quando os equipamentos são mantidos em boas condições, a probabilidade de falhas inesperadas diminui significativamente. Isso significa que as empresas podem evitar gastos elevados com reparos emergenciais e substituições de equipamentos. Além disso, a manutenção regular ajuda a identificar problemas em potencial antes que se tornem críticos, permitindo que as empresas planejem e orcem adequadamente para as intervenções necessárias.
Outro aspecto importante da manutenção preventiva é a melhoria da eficiência operacional. Equipamentos bem mantidos operam de maneira mais eficiente, resultando em um desempenho superior. Isso é especialmente relevante em ambientes industriais, onde a eficiência pode impactar diretamente a produtividade. Por exemplo, uma máquina que não passa por manutenção regular pode apresentar um desempenho abaixo do ideal, levando a atrasos na produção e, consequentemente, a perdas financeiras.
A segurança também é um fator crucial a ser considerado. Equipamentos mal conservados podem representar riscos significativos para os operadores e para o ambiente de trabalho. A manutenção preventiva ajuda a garantir que todos os dispositivos estejam funcionando corretamente e de acordo com as normas de segurança. Isso não apenas protege os funcionários, mas também reduz a responsabilidade legal da empresa em caso de acidentes relacionados a falhas de equipamentos.
Além disso, a manutenção preventiva contribui para a preservação do valor dos ativos. Equipamentos que recebem cuidados regulares tendem a manter seu valor de mercado por mais tempo. Isso é especialmente importante para empresas que podem precisar vender ou alugar seus equipamentos no futuro. Um histórico de manutenção adequada pode ser um diferencial significativo na hora de negociar a venda ou locação de um ativo.
Outro ponto a ser destacado é a importância da calibração dos equipamentos, que deve ser parte integrante da manutenção preventiva. A calibração garante que os dispositivos estejam operando dentro das especificações corretas, o que é fundamental para a precisão e a qualidade dos resultados. Equipamentos mal calibrados podem levar a medições imprecisas, afetando a qualidade do produto final e, em última análise, a satisfação do cliente. Para garantir a calibração adequada, é recomendável contar com uma Empresa de calibração especializada, que possa realizar esse serviço de forma eficiente e confiável.
Além dos benefícios diretos, a manutenção preventiva também pode ter um impacto positivo na moral dos funcionários. Quando os equipamentos estão em boas condições de funcionamento, os operadores se sentem mais seguros e confiantes em suas tarefas. Isso pode resultar em um ambiente de trabalho mais produtivo e motivado, onde os funcionários se sentem valorizados e apoiados pela empresa.
Por fim, a manutenção preventiva é uma prática que se alinha com a sustentabilidade. Ao prolongar a vida útil dos equipamentos e reduzir a necessidade de substituições frequentes, as empresas podem minimizar seu impacto ambiental. Isso é especialmente relevante em um momento em que a responsabilidade ambiental é uma preocupação crescente para consumidores e investidores. Implementar um programa de manutenção preventiva pode ser uma maneira eficaz de demonstrar o compromisso da empresa com a sustentabilidade e a responsabilidade social.
Em resumo, a manutenção preventiva é uma prática essencial para qualquer empresa que dependa de equipamentos para suas operações. Os benefícios incluem a redução de custos, a melhoria da eficiência, a segurança dos funcionários, a preservação do valor dos ativos e a promoção de um ambiente de trabalho positivo. Além disso, a calibração adequada dos equipamentos deve ser parte integrante desse processo, garantindo que todos os dispositivos operem dentro das especificações corretas. Investir em manutenção preventiva é, portanto, uma decisão estratégica que pode trazer retornos significativos a longo prazo.
Métodos Eficazes de Calibração de Equipamentos
A calibração de equipamentos é um processo fundamental para garantir a precisão e a confiabilidade das medições realizadas por dispositivos utilizados em diversas indústrias. A calibração adequada não apenas assegura que os equipamentos estejam funcionando dentro das especificações, mas também contribui para a qualidade do produto final e a segurança operacional. Neste artigo, abordaremos métodos eficazes de calibração de equipamentos, destacando as melhores práticas e a importância de contar com profissionais qualificados.
Um dos métodos mais comuns de calibração é a calibração comparativa. Este método envolve a comparação das medições do equipamento em questão com um padrão de referência conhecido e rastreável. O padrão de referência deve ter uma precisão superior à do equipamento que está sendo calibrado. Durante o processo, as medições do equipamento são registradas e comparadas com as do padrão. Se houver discrepâncias, ajustes são feitos para garantir que o equipamento esteja dentro das tolerâncias especificadas. Este método é amplamente utilizado em laboratórios e indústrias que exigem alta precisão nas medições.
Outro método eficaz é a calibração em campo, que é realizada no local onde o equipamento está instalado. Este tipo de calibração é especialmente útil para equipamentos que não podem ser facilmente transportados para um laboratório. A calibração em campo permite que os técnicos realizem ajustes e verificações sem a necessidade de desinstalar o equipamento. É importante que a calibração em campo seja realizada por profissionais experientes, que possam garantir que as condições ambientais não afetem as medições. Além disso, a calibração em campo deve seguir os mesmos princípios da calibração comparativa, utilizando padrões de referência adequados.
A calibração por meio de software também tem ganhado destaque, especialmente em equipamentos modernos que possuem interfaces digitais. Muitos dispositivos vêm com software de calibração que permite que os usuários realizem ajustes e verifiquem a precisão das medições diretamente no computador. Este método pode ser muito eficiente, pois permite que os usuários monitorem e ajustem os equipamentos em tempo real. No entanto, é crucial que o software utilizado seja confiável e que os usuários sejam treinados para operar as ferramentas de calibração corretamente.
Além dos métodos mencionados, a calibração em múltiplos pontos é uma prática recomendada para garantir a precisão em toda a faixa de operação do equipamento. Em vez de calibrar apenas em um único ponto, a calibração em múltiplos pontos envolve a verificação das medições em diferentes intervalos. Isso é especialmente importante para equipamentos que operam em uma ampla gama de condições. A calibração em múltiplos pontos ajuda a identificar não apenas desvios em medições, mas também tendências que podem indicar problemas futuros. Essa abordagem abrangente é essencial para garantir a confiabilidade a longo prazo dos equipamentos.
Outro aspecto importante a considerar é a frequência da calibração. A determinação da frequência ideal para a calibração depende de vários fatores, incluindo a natureza do equipamento, a frequência de uso e as condições ambientais. Equipamentos que são utilizados com frequência ou que operam em ambientes adversos podem exigir calibrações mais frequentes. Por outro lado, equipamentos que são usados esporadicamente podem ter intervalos de calibração mais longos. É fundamental que as empresas desenvolvam um cronograma de calibração que atenda às suas necessidades específicas e que seja seguido rigorosamente.
Contar com uma Empresa de calibração de equipamentos especializada é essencial para garantir que todos esses métodos sejam aplicados corretamente. Profissionais qualificados possuem o conhecimento e a experiência necessários para realizar calibrações de forma eficaz, utilizando equipamentos e padrões de referência adequados. Além disso, uma empresa especializada pode oferecer suporte contínuo, ajudando as empresas a manterem seus equipamentos em conformidade com as normas e regulamentos aplicáveis.
Por fim, é importante ressaltar que a documentação é uma parte crucial do processo de calibração. Todos os resultados de calibração devem ser registrados e mantidos em arquivos para referência futura. Isso não apenas ajuda a garantir a rastreabilidade, mas também fornece um histórico que pode ser útil em auditorias e inspeções. A documentação deve incluir informações sobre os padrões utilizados, os resultados das medições, os ajustes realizados e a data da calibração. Manter registros precisos é fundamental para garantir a conformidade e a qualidade dos processos.
Em resumo, a calibração de equipamentos é um processo vital que deve ser realizado de maneira sistemática e eficaz. Métodos como calibração comparativa, calibração em campo, calibração por software e calibração em múltiplos pontos são essenciais para garantir a precisão e a confiabilidade das medições. A frequência da calibração deve ser determinada com base nas necessidades específicas de cada equipamento, e contar com uma empresa especializada é fundamental para garantir que todos os procedimentos sejam seguidos corretamente. Com a abordagem adequada, as empresas podem garantir que seus equipamentos operem de maneira eficiente e segura, contribuindo para a qualidade do produto final e a satisfação do cliente.
Frequência Recomendada para Manutenção e Calibração
A frequência recomendada para manutenção e calibração de equipamentos é um aspecto crucial para garantir a eficiência e a durabilidade dos dispositivos utilizados em diversas indústrias. A manutenção e a calibração regulares não apenas asseguram que os equipamentos operem dentro das especificações, mas também ajudam a prevenir falhas inesperadas que podem resultar em custos elevados e interrupções nas operações. Neste artigo, discutiremos a importância de estabelecer uma frequência adequada para esses processos e como determinar a melhor abordagem para cada tipo de equipamento.
Um dos principais fatores a considerar ao determinar a frequência de manutenção e calibração é a natureza do equipamento. Equipamentos que operam em ambientes adversos, como fábricas com altas temperaturas, umidade ou poeira, podem exigir manutenção e calibração mais frequentes. Por outro lado, dispositivos que são utilizados em condições controladas e limpas podem ter intervalos mais longos entre as manutenções. Portanto, é fundamental avaliar as condições em que o equipamento opera para estabelecer um cronograma adequado.
A frequência de uso do equipamento também desempenha um papel importante na determinação da necessidade de manutenção e calibração. Equipamentos que são utilizados diariamente ou em turnos contínuos tendem a sofrer mais desgaste e, portanto, podem exigir manutenção mais frequente. Em contrapartida, dispositivos que são utilizados esporadicamente podem ter intervalos de manutenção mais longos. É recomendável que as empresas desenvolvam um cronograma de manutenção baseado na intensidade de uso de cada equipamento, garantindo que todos os dispositivos recebam a atenção necessária.
Além disso, a complexidade do equipamento deve ser considerada. Equipamentos mais complexos, que possuem múltiplos componentes e sistemas interligados, podem exigir calibrações e manutenções mais frequentes. Isso se deve ao fato de que, em sistemas complexos, uma falha em um componente pode afetar o desempenho geral do equipamento. Portanto, é importante que as empresas realizem uma análise detalhada da complexidade de seus dispositivos e ajustem a frequência de manutenção e calibração de acordo.
Outro aspecto a ser considerado é a recomendação do fabricante. A maioria dos fabricantes fornece diretrizes específicas sobre a frequência de manutenção e calibração para seus equipamentos. Essas recomendações são baseadas em testes e experiências acumuladas ao longo do tempo e devem ser seguidas rigorosamente. Ignorar as orientações do fabricante pode resultar em problemas de desempenho e até mesmo na anulação da garantia do equipamento. Portanto, é essencial consultar o manual do usuário e seguir as diretrizes fornecidas.
Um cronograma de manutenção e calibração deve ser documentado e monitorado de forma sistemática. As empresas devem manter registros detalhados de todas as manutenções e calibrações realizadas, incluindo datas, resultados e quaisquer ajustes feitos. Isso não apenas ajuda a garantir a rastreabilidade, mas também fornece um histórico que pode ser útil em auditorias e inspeções. A documentação adequada é fundamental para garantir a conformidade com as normas e regulamentos aplicáveis.
Além disso, a implementação de um sistema de gestão de manutenção pode ser uma solução eficaz para monitorar a frequência de manutenção e calibração. Esses sistemas permitem que as empresas programem manutenções, acompanhem os prazos e gerenciem os registros de forma eficiente. Com um sistema de gestão, as empresas podem garantir que as manutenções e calibrações sejam realizadas dentro dos prazos estabelecidos, minimizando o risco de falhas e interrupções nas operações.
É importante ressaltar que a calibração deve ser realizada em intervalos regulares, independentemente do uso do equipamento. A calibração é essencial para garantir que os dispositivos estejam operando dentro das especificações corretas e para evitar medições imprecisas que podem afetar a qualidade do produto final. A frequência da calibração pode variar de acordo com o tipo de equipamento, mas, em geral, recomenda-se que a calibração seja realizada pelo menos uma vez por ano. Para equipamentos críticos, como aqueles utilizados em laboratórios de controle de qualidade, a calibração pode ser necessária a cada três ou seis meses.
Contar com um Serviço de calibração especializado é fundamental para garantir que todos os processos sejam realizados de forma adequada. Profissionais qualificados possuem o conhecimento e a experiência necessários para realizar calibrações de forma eficaz, utilizando equipamentos e padrões de referência adequados. Além disso, uma empresa especializada pode oferecer suporte contínuo, ajudando as empresas a manterem seus equipamentos em conformidade com as normas e regulamentos aplicáveis.
Em resumo, a frequência recomendada para manutenção e calibração de equipamentos deve ser determinada com base em vários fatores, incluindo a natureza do equipamento, a frequência de uso, a complexidade do dispositivo e as recomendações do fabricante. Manter um cronograma de manutenção documentado e monitorado é essencial para garantir a eficiência e a durabilidade dos equipamentos. A implementação de um sistema de gestão de manutenção pode facilitar esse processo, permitindo que as empresas programem e acompanhem as manutenções e calibrações de forma eficaz. Com a abordagem adequada, as empresas podem garantir que seus equipamentos operem de maneira eficiente e segura, contribuindo para a qualidade do produto final e a satisfação do cliente.
Erros Comuns na Manutenção e Calibração de Equipamentos
A manutenção e calibração de equipamentos são processos essenciais para garantir a eficiência e a precisão dos dispositivos utilizados em diversas indústrias. No entanto, existem erros comuns que podem comprometer a eficácia dessas práticas, resultando em falhas operacionais e custos adicionais. Neste artigo, abordaremos os principais erros cometidos durante a manutenção e calibração de equipamentos, destacando a importância de evitá-los para garantir a qualidade e a segurança das operações.
Um dos erros mais frequentes é a falta de um cronograma de manutenção bem definido. Muitas empresas não estabelecem um plano claro para a manutenção e calibração de seus equipamentos, o que pode levar a atrasos e negligência. Sem um cronograma, é fácil esquecer de realizar manutenções regulares, o que pode resultar em falhas inesperadas e custos elevados com reparos emergenciais. É fundamental que as empresas desenvolvam um cronograma de manutenção baseado nas recomendações do fabricante e nas condições de operação dos equipamentos.
Outro erro comum é a utilização de padrões de calibração inadequados. A calibração deve ser realizada utilizando padrões de referência que sejam rastreáveis e que atendam às especificações do equipamento. Quando padrões inadequados são utilizados, as medições podem se tornar imprecisas, comprometendo a qualidade do produto final. É essencial que as empresas utilizem padrões de calibração apropriados e que verifiquem regularmente a precisão desses padrões para garantir resultados confiáveis.
A falta de treinamento adequado para os profissionais responsáveis pela manutenção e calibração também é um erro significativo. Muitas vezes, os técnicos não recebem o treinamento necessário para realizar as tarefas de forma eficaz, o que pode resultar em erros durante o processo. É importante que as empresas invistam em capacitação e treinamento contínuo para suas equipes, garantindo que todos os envolvidos na manutenção e calibração estejam atualizados sobre as melhores práticas e procedimentos.
Além disso, a negligência na documentação dos processos de manutenção e calibração é um erro que pode ter consequências graves. A documentação adequada é fundamental para garantir a rastreabilidade e a conformidade com as normas e regulamentos aplicáveis. Quando as empresas não mantêm registros detalhados das manutenções e calibrações realizadas, podem enfrentar dificuldades em auditorias e inspeções. É essencial que todas as atividades sejam registradas, incluindo datas, resultados e ajustes realizados, para garantir a transparência e a responsabilidade.
Outro erro comum é a falta de comunicação entre as equipes envolvidas na manutenção e calibração. Muitas vezes, as informações sobre o estado dos equipamentos e as necessidades de manutenção não são compartilhadas de forma eficaz entre os departamentos. Isso pode levar a mal-entendidos e à realização de manutenções desnecessárias ou à omissão de tarefas críticas. A comunicação clara e eficaz é fundamental para garantir que todos os envolvidos estejam cientes das necessidades de manutenção e calibração dos equipamentos.
A escolha inadequada de ferramentas e equipamentos para a manutenção e calibração também pode comprometer os resultados. Utilizar ferramentas que não são apropriadas para o tipo de equipamento ou que estão em más condições pode resultar em medições imprecisas e danos aos dispositivos. É importante que as empresas verifiquem regularmente as condições das ferramentas utilizadas e que garantam que estão utilizando os equipamentos corretos para cada tarefa.
Além disso, a falta de atenção às condições ambientais durante a calibração é um erro que pode afetar a precisão das medições. Fatores como temperatura, umidade e vibrações podem influenciar os resultados da calibração. É fundamental que as calibrações sejam realizadas em condições controladas e que os técnicos estejam cientes das influências ambientais que podem afetar os resultados. Realizar calibrações em ambientes inadequados pode levar a medições imprecisas e comprometer a qualidade do produto final.
Por fim, a subestimação da importância da calibração regular é um erro que pode ter consequências sérias. Muitas empresas acreditam que a calibração é uma tarefa única e que, uma vez realizada, não precisa ser repetida. No entanto, a calibração deve ser um processo contínuo, realizado em intervalos regulares, para garantir que os equipamentos permaneçam precisos ao longo do tempo. Ignorar a necessidade de calibração regular pode resultar em medições imprecisas e, consequentemente, em produtos de baixa qualidade.
Contar com uma Empresa de calibração de instrumentos de medição especializada é fundamental para evitar esses erros comuns. Profissionais qualificados possuem o conhecimento e a experiência necessários para realizar manutenções e calibrações de forma eficaz, utilizando equipamentos e padrões de referência adequados. Além disso, uma empresa especializada pode oferecer suporte contínuo, ajudando as empresas a manterem seus equipamentos em conformidade com as normas e regulamentos aplicáveis.
Em resumo, evitar erros comuns na manutenção e calibração de equipamentos é essencial para garantir a eficiência e a precisão dos dispositivos utilizados nas operações. Estabelecer um cronograma de manutenção, utilizar padrões adequados, investir em treinamento, manter documentação precisa, promover comunicação eficaz, escolher ferramentas apropriadas, considerar as condições ambientais e realizar calibrações regulares são práticas fundamentais para garantir a qualidade e a segurança das operações. Com a abordagem correta, as empresas podem maximizar a vida útil de seus equipamentos e garantir a satisfação do cliente.
Em conclusão, a manutenção preventiva e a calibração de equipamentos são essenciais para assegurar a eficiência, a segurança e a durabilidade dos dispositivos utilizados nas operações industriais. Ao implementar práticas adequadas, como o estabelecimento de cronogramas de manutenção, a utilização de padrões de calibração apropriados e o investimento em treinamento para os profissionais envolvidos, as empresas podem evitar falhas inesperadas e reduzir custos operacionais. Além disso, a documentação precisa e a comunicação eficaz entre as equipes são fundamentais para garantir a rastreabilidade e a conformidade com as normas. Com um compromisso contínuo com a manutenção e calibração, as organizações não apenas prolongam a vida útil de seus equipamentos, mas também asseguram a qualidade de seus produtos e a satisfação de seus clientes.