Calibração Dimensional: A Importância para a Precisão na Indústria
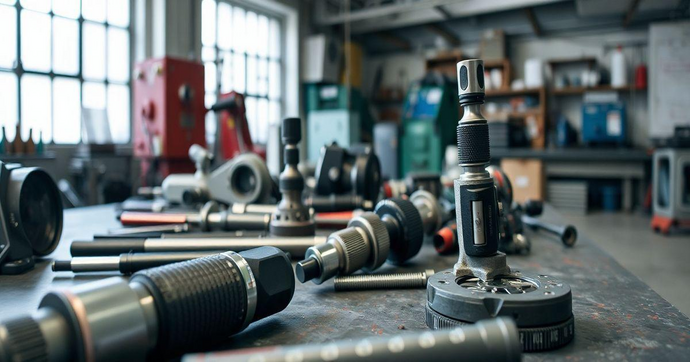
Por: Mauricio - 21 de Janeiro de 2025
A calibração dimensional é um processo fundamental na indústria, garantindo que os equipamentos e instrumentos de medição estejam precisos e confiáveis. Com a crescente demanda por qualidade e precisão, entender a calibração dimensional se torna essencial para empresas que buscam otimizar seus processos e garantir a satisfação do cliente. Neste artigo, exploraremos os conceitos, métodos e benefícios da calibração dimensional, além de fornecer orientações práticas para sua implementação eficaz.
O que é Calibração Dimensional e sua Relevância na Indústria
A calibração dimensional é um processo que visa garantir a precisão e a exatidão de instrumentos de medição, assegurando que eles forneçam resultados confiáveis e consistentes. Este procedimento é essencial em diversos setores industriais, onde a precisão nas medições pode impactar diretamente a qualidade do produto final e a segurança dos processos. A calibração envolve a comparação de um instrumento de medição com um padrão de referência, que é reconhecido e validado, para identificar e corrigir possíveis desvios.
Na prática, a calibração dimensional pode ser aplicada a uma ampla gama de instrumentos, incluindo micrômetros, paquímetros, goniômetros e máquinas de medição por coordenadas (CMM). Cada um desses instrumentos desempenha um papel crucial na medição de dimensões, ângulos e outras características físicas de peças e componentes. A precisão dessas medições é vital para garantir que os produtos atendam às especificações técnicas e aos padrões de qualidade exigidos pelo mercado.
A relevância da calibração dimensional na indústria não pode ser subestimada. Em um ambiente de produção, a utilização de instrumentos não calibrados pode resultar em erros de medição que, por sua vez, podem levar a defeitos nos produtos, retrabalhos, desperdícios e até mesmo riscos à segurança. Por exemplo, em setores como a indústria automotiva e aeroespacial, onde a precisão é crítica, um pequeno erro de medição pode comprometer a integridade de um componente e, consequentemente, a segurança do usuário final.
Além disso, a calibração dimensional é um requisito fundamental para a conformidade com normas e certificações de qualidade, como ISO 9001 e ISO/TS 16949. Essas normas estabelecem diretrizes rigorosas para a gestão da qualidade e a melhoria contínua dos processos, e a calibração de instrumentos de medição é uma parte integral desse sistema. As empresas que não realizam a calibração adequada podem enfrentar problemas de auditoria, perda de certificações e, em última instância, danos à sua reputação no mercado.
Outro aspecto importante da calibração dimensional é a sua contribuição para a eficiência operacional. Ao garantir que os instrumentos de medição estejam sempre precisos, as empresas podem reduzir o tempo de inatividade e os custos associados a retrabalhos e desperdícios. Isso se traduz em uma produção mais eficiente e em um melhor aproveitamento dos recursos disponíveis. Além disso, a calibração regular pode ajudar a identificar problemas potenciais nos equipamentos antes que eles se tornem críticos, permitindo que as empresas realizem manutenções preventivas e evitem paradas inesperadas.
É importante ressaltar que a calibração dimensional deve ser realizada por profissionais qualificados e em ambientes controlados, onde as condições de temperatura, umidade e vibração sejam monitoradas. A escolha de uma Empresa de calibração confiável é fundamental para garantir que os serviços prestados atendam aos padrões exigidos e que os resultados sejam válidos e reconhecidos. Essas empresas possuem equipamentos e técnicas adequadas para realizar calibrações de forma precisa e eficiente, assegurando a qualidade dos instrumentos de medição utilizados na produção.
Em resumo, a calibração dimensional é um processo essencial que garante a precisão e a confiabilidade dos instrumentos de medição utilizados na indústria. Sua relevância se estende desde a conformidade com normas de qualidade até a eficiência operacional e a segurança dos produtos. Investir em calibração não é apenas uma questão de conformidade, mas uma estratégia inteligente para melhorar a qualidade e a competitividade no mercado. Portanto, as empresas devem priorizar a calibração regular de seus instrumentos de medição como parte de sua estratégia de gestão da qualidade e melhoria contínua.
2. Principais Métodos de Calibração Dimensional
A calibração dimensional é um processo que pode ser realizado por meio de diferentes métodos, cada um adequado a tipos específicos de instrumentos de medição e aplicações industriais. A escolha do método de calibração depende de diversos fatores, incluindo o tipo de instrumento, a precisão necessária e as condições de operação. Neste artigo, abordaremos os principais métodos de calibração dimensional utilizados na indústria, destacando suas características e aplicações.
Um dos métodos mais comuns de calibração é a calibração por comparação. Neste método, o instrumento a ser calibrado é comparado a um padrão de referência que possui uma precisão conhecida. O padrão pode ser um instrumento de medição de alta precisão ou um dispositivo de calibração específico. Durante o processo, as medições realizadas pelo instrumento em teste são comparadas com as medições do padrão, permitindo identificar desvios e realizar os ajustes necessários. Este método é amplamente utilizado para calibrações de micrômetros, paquímetros e outros instrumentos de medição lineares.
Outro método importante é a calibração por ajuste. Neste caso, o instrumento é ajustado diretamente para que suas medições correspondam aos valores do padrão de referência. Esse método é frequentemente utilizado em instrumentos que possuem mecanismos de ajuste interno, como calibradores eletrônicos. A calibração por ajuste é particularmente útil quando o instrumento apresenta desvios significativos que precisam ser corrigidos. É importante ressaltar que, após o ajuste, o instrumento deve ser submetido a um novo teste de comparação para garantir que as medições estejam dentro das especificações desejadas.
A calibração por verificação é um método que envolve a realização de medições em um conjunto de padrões conhecidos. Neste caso, o instrumento a ser calibrado é utilizado para medir dimensões de padrões que possuem valores previamente estabelecidos. As medições obtidas são então comparadas com os valores conhecidos, permitindo verificar a precisão do instrumento. Este método é especialmente útil para instrumentos que não podem ser ajustados, como máquinas de medição por coordenadas (CMM). A calibração por verificação é uma prática comum em laboratórios de metrologia e em ambientes de produção onde a precisão é crítica.
Além desses métodos, a calibração dimensional também pode ser realizada por meio de técnicas de calibração em campo. Este método é utilizado quando a calibração precisa ser realizada no local de uso do instrumento, como em fábricas ou oficinas. A calibração em campo é prática e conveniente, mas pode apresentar desafios, como variações nas condições ambientais que podem afetar as medições. Para garantir a precisão, é fundamental que a calibração em campo seja realizada por profissionais qualificados e com equipamentos adequados.
Outro método que merece destaque é a calibração por meio de software de simulação. Com o avanço da tecnologia, muitos instrumentos modernos agora vêm equipados com software que permite simular medições e realizar calibrações virtuais. Esse método é especialmente útil para instrumentos eletrônicos e digitais, onde a calibração pode ser realizada de forma rápida e eficiente. No entanto, é importante que a calibração por software seja complementada por verificações físicas regulares para garantir a precisão a longo prazo.
Independentemente do método escolhido, a calibração dimensional deve ser realizada por profissionais qualificados e em ambientes controlados. A escolha de uma Empresa de calibração de equipamentos confiável é fundamental para garantir que os serviços prestados atendam aos padrões exigidos e que os resultados sejam válidos e reconhecidos. Essas empresas possuem equipamentos e técnicas adequadas para realizar calibrações de forma precisa e eficiente, assegurando a qualidade dos instrumentos de medição utilizados na produção.
Além disso, é importante ressaltar que a calibração deve ser realizada regularmente, de acordo com as recomendações do fabricante e as normas de qualidade aplicáveis. A frequência da calibração pode variar dependendo do tipo de instrumento, da intensidade de uso e das condições ambientais. A manutenção de um cronograma de calibração adequado é essencial para garantir que os instrumentos permaneçam precisos e confiáveis ao longo do tempo.
Em conclusão, os principais métodos de calibração dimensional incluem calibração por comparação, ajuste, verificação, calibração em campo e calibração por software de simulação. Cada um desses métodos possui suas características e aplicações específicas, e a escolha do método adequado depende das necessidades da indústria e do tipo de instrumento a ser calibrado. Investir em calibração dimensional é uma estratégia inteligente para garantir a qualidade e a precisão dos processos industriais, contribuindo para a eficiência operacional e a satisfação do cliente.
3. Equipamentos Utilizados na Calibração Dimensional
A calibração dimensional é um processo crítico que requer o uso de equipamentos especializados para garantir a precisão e a confiabilidade das medições. Esses equipamentos são projetados para medir, comparar e ajustar instrumentos de medição, assegurando que eles operem dentro das especificações exigidas. Neste artigo, abordaremos os principais equipamentos utilizados na calibração dimensional, suas funções e a importância de cada um deles no processo de calibração.
Um dos equipamentos mais comuns na calibração dimensional é o calibrador de altura. Este instrumento é utilizado para medir a altura de peças e componentes com alta precisão. O calibrador de altura é equipado com uma régua vertical e um cursor que se move ao longo da régua, permitindo medições exatas. Ele é amplamente utilizado em indústrias que exigem medições precisas, como a automotiva e a aeroespacial. A calibração deste equipamento é essencial para garantir que as medições de altura sejam confiáveis e consistentes.
Outro equipamento fundamental é o micrômetro, que é utilizado para medir dimensões externas, internas e profundidades de peças com alta precisão. Os micrômetros são conhecidos por sua capacidade de realizar medições em escalas muito pequenas, geralmente em milímetros ou polegadas. A calibração de micrômetros é crucial, pois um pequeno erro pode resultar em grandes desvios nas dimensões finais das peças. A calibração é realizada comparando o micrômetro com padrões de referência, garantindo que ele forneça medições exatas.
Os paquímetros também são equipamentos essenciais na calibração dimensional. Eles são utilizados para medir a largura, a profundidade e a espessura de objetos com precisão. Os paquímetros podem ser analógicos ou digitais, e a calibração é necessária para garantir que as medições estejam corretas. A calibração de paquímetros envolve a comparação com padrões de referência e a verificação de que as escalas estejam alinhadas corretamente. A precisão dos paquímetros é vital em diversas aplicações industriais, desde a fabricação de peças até a inspeção de qualidade.
As máquinas de medição por coordenadas (CMM) são outro equipamento avançado utilizado na calibração dimensional. Essas máquinas são projetadas para medir a geometria de um objeto em três dimensões, utilizando um sistema de coordenadas. As CMMs podem ser equipadas com diferentes tipos de sondas, como sondas táteis ou ópticas, para realizar medições precisas. A calibração de CMMs é complexa e envolve a verificação de sua precisão em relação a padrões de referência. A calibração regular é essencial para garantir que as medições realizadas por essas máquinas sejam confiáveis e atendam aos requisitos de qualidade.
Além dos instrumentos mencionados, existem também os goniômetros, que são utilizados para medir ângulos com precisão. Esses dispositivos são essenciais em indústrias que trabalham com peças que exigem ângulos exatos, como a indústria de moldes e matrizes. A calibração de goniômetros é realizada comparando suas medições com padrões de ângulo conhecidos, garantindo que os resultados sejam precisos e consistentes.
Os calibradores eletrônicos também desempenham um papel importante na calibração dimensional. Esses dispositivos são utilizados para medir e ajustar instrumentos eletrônicos, como multímetros e osciloscópios. A calibração de equipamentos eletrônicos é crucial para garantir que eles operem dentro das especificações e forneçam medições precisas. O uso de calibradores eletrônicos permite que as empresas mantenham a precisão em seus processos de medição e controle de qualidade.
Para garantir a eficácia da calibração, é fundamental que os equipamentos utilizados sejam mantidos em boas condições e calibrados regularmente. A escolha de uma Serviço de calibração confiável é essencial para assegurar que os instrumentos de medição sejam calibrados de acordo com os padrões exigidos. Essas empresas possuem equipamentos e técnicas adequadas para realizar calibrações de forma precisa e eficiente, assegurando a qualidade dos instrumentos utilizados na produção.
Além disso, a calibração deve ser realizada em ambientes controlados, onde as condições de temperatura, umidade e vibração sejam monitoradas. Isso é importante para garantir que os resultados da calibração sejam válidos e que os instrumentos permaneçam precisos ao longo do tempo. A manutenção de um cronograma de calibração adequado é essencial para garantir que os instrumentos permaneçam confiáveis e atendam às exigências do mercado.
Em resumo, os principais equipamentos utilizados na calibração dimensional incluem calibradores de altura, micrômetros, paquímetros, máquinas de medição por coordenadas, goniômetros e calibradores eletrônicos. Cada um desses equipamentos desempenha um papel crucial na garantia da precisão e confiabilidade das medições. Investir em calibração dimensional e na manutenção adequada dos equipamentos é uma estratégia inteligente para garantir a qualidade e a eficiência dos processos industriais, contribuindo para a satisfação do cliente e a competitividade no mercado.
4. Passos para Realizar a Calibração Dimensional
A calibração dimensional é um processo essencial para garantir a precisão e a confiabilidade dos instrumentos de medição utilizados na indústria. Realizar a calibração de forma adequada envolve uma série de passos que devem ser seguidos rigorosamente. Neste artigo, abordaremos os principais passos para realizar a calibração dimensional, assegurando que os instrumentos estejam sempre dentro das especificações exigidas.
O primeiro passo na calibração dimensional é a preparação do ambiente. É fundamental que a calibração seja realizada em um ambiente controlado, onde as condições de temperatura, umidade e vibração sejam monitoradas. Essas condições podem afetar as medições e, portanto, devem ser mantidas dentro de limites aceitáveis. Além disso, é importante garantir que o local esteja limpo e livre de contaminantes que possam interferir nas medições. A preparação do ambiente é crucial para obter resultados precisos e confiáveis.
Após a preparação do ambiente, o próximo passo é reunir os equipamentos necessários para a calibração. Isso inclui não apenas o instrumento que será calibrado, mas também os padrões de referência que serão utilizados para comparação. Os padrões devem ser certificados e reconhecidos, garantindo que suas medições sejam válidas. Além disso, é importante ter à disposição todos os acessórios e ferramentas necessárias para a calibração, como suportes, goniômetros e dispositivos de fixação. A organização e a disponibilidade dos equipamentos são essenciais para um processo de calibração eficiente.
O terceiro passo envolve a verificação do instrumento a ser calibrado. Antes de iniciar a calibração, é importante realizar uma inspeção visual do instrumento para identificar possíveis danos ou desgastes. Verifique se todas as partes móveis estão funcionando corretamente e se não há sujeira ou obstruções que possam afetar as medições. Caso o instrumento apresente problemas, é recomendável realizar os reparos necessários antes de prosseguir com a calibração. Essa verificação inicial ajuda a garantir que o instrumento esteja em condições adequadas para a calibração.
Uma vez que o instrumento foi verificado, o próximo passo é realizar a calibração propriamente dita. Este processo pode variar dependendo do tipo de instrumento e do método de calibração escolhido. Em geral, a calibração envolve a comparação das medições do instrumento com as medições do padrão de referência. Para instrumentos analógicos, como micrômetros e paquímetros, as medições devem ser registradas e comparadas com os valores do padrão. Para instrumentos digitais, a calibração pode envolver a configuração de parâmetros e ajustes internos. É importante seguir as instruções do fabricante e as normas de calibração aplicáveis durante este processo.
Após a calibração, o próximo passo é documentar os resultados. A documentação é uma parte crucial do processo de calibração, pois fornece um registro das medições realizadas e dos ajustes feitos. É importante registrar informações como a data da calibração, os valores medidos, os valores do padrão de referência e quaisquer ajustes realizados no instrumento. Essa documentação é essencial para garantir a rastreabilidade e a conformidade com as normas de qualidade. Além disso, a documentação pode ser útil para futuras calibrações e auditorias.
O sexto passo envolve a realização de testes de verificação após a calibração. Após ajustar o instrumento, é importante realizar medições de verificação para garantir que ele esteja operando dentro das especificações. Isso envolve medir padrões conhecidos e comparar os resultados com os valores esperados. Se as medições estiverem dentro dos limites aceitáveis, a calibração pode ser considerada bem-sucedida. Caso contrário, pode ser necessário repetir o processo de calibração ou realizar ajustes adicionais.
Por fim, o último passo é manter um cronograma de calibração regular. A calibração não deve ser vista como uma atividade única, mas sim como parte de um programa contínuo de manutenção e controle de qualidade. É importante estabelecer um cronograma de calibração com base nas recomendações do fabricante, na frequência de uso do instrumento e nas normas de qualidade aplicáveis. A manutenção de um cronograma adequado ajuda a garantir que os instrumentos permaneçam precisos e confiáveis ao longo do tempo.
Para garantir a eficácia da calibração, é fundamental contar com a expertise de uma Empresa de calibração de instrumentos de medição confiável. Essas empresas possuem equipamentos e técnicas adequadas para realizar calibrações de forma precisa e eficiente, assegurando a qualidade dos instrumentos utilizados na produção. Além disso, profissionais qualificados podem oferecer orientações sobre as melhores práticas de calibração e manutenção, contribuindo para a eficiência operacional e a conformidade com as normas de qualidade.
Em resumo, os passos para realizar a calibração dimensional incluem a preparação do ambiente, a reunião dos equipamentos necessários, a verificação do instrumento, a realização da calibração, a documentação dos resultados, a realização de testes de verificação e a manutenção de um cronograma de calibração regular. Seguir esses passos rigorosamente é essencial para garantir a precisão e a confiabilidade dos instrumentos de medição, contribuindo para a qualidade e a eficiência dos processos industriais.
5. Benefícios da Calibração Dimensional para a Qualidade do Produto
A calibração dimensional é um processo essencial que traz uma série de benefícios significativos para a qualidade do produto em diversos setores industriais. A precisão nas medições é fundamental para garantir que os produtos atendam às especificações e normas de qualidade exigidas pelo mercado. Neste artigo, exploraremos os principais benefícios da calibração dimensional e como ela contribui para a melhoria da qualidade do produto.
Um dos principais benefícios da calibração dimensional é a redução de erros de medição. Instrumentos de medição não calibrados podem apresentar desvios que resultam em medições imprecisas. Esses erros podem levar à produção de peças fora das especificações, resultando em retrabalhos, desperdícios e até mesmo falhas de produto. Ao realizar a calibração regularmente, as empresas podem garantir que seus instrumentos estejam sempre precisos, minimizando a probabilidade de erros e melhorando a qualidade geral dos produtos fabricados.
Outro benefício importante é a conformidade com normas e regulamentos. Muitas indústrias operam sob rigorosos padrões de qualidade, como ISO 9001 e ISO/TS 16949. A calibração dimensional é um requisito fundamental para atender a essas normas, pois assegura que os instrumentos de medição estejam funcionando corretamente. A conformidade com as normas não apenas melhora a qualidade do produto, mas também aumenta a confiança dos clientes e a reputação da empresa no mercado. Empresas que demonstram compromisso com a qualidade são mais propensas a conquistar e manter a lealdade dos clientes.
A calibração dimensional também contribui para a eficiência operacional. Quando os instrumentos de medição estão calibrados e funcionando corretamente, as empresas podem otimizar seus processos de produção. Isso significa menos tempo gasto em retrabalhos e correções, resultando em uma produção mais eficiente e econômica. Além disso, a calibração regular ajuda a identificar problemas potenciais nos equipamentos antes que eles se tornem críticos, permitindo que as empresas realizem manutenções preventivas e evitem paradas inesperadas. A eficiência operacional não apenas melhora a qualidade do produto, mas também reduz os custos operacionais.
Outro aspecto relevante é a valorização do produto. Produtos que atendem a altos padrões de qualidade são mais valorizados no mercado. A calibração dimensional garante que as peças e componentes sejam fabricados com precisão, o que pode resultar em produtos finais de maior qualidade. Isso é especialmente importante em setores como a indústria automotiva e aeroespacial, onde a precisão é crítica. Produtos de alta qualidade não apenas atraem mais clientes, mas também podem justificar preços mais altos, aumentando a margem de lucro da empresa.
A calibração dimensional também desempenha um papel crucial na segurança do produto. Em indústrias onde a segurança é uma preocupação primordial, como a farmacêutica e a alimentícia, a precisão nas medições é vital para garantir que os produtos sejam seguros para o consumo. A calibração regular dos instrumentos de medição ajuda a garantir que os produtos atendam aos padrões de segurança e qualidade, protegendo os consumidores e evitando possíveis problemas legais para a empresa. A segurança do produto é um aspecto que não pode ser negligenciado, e a calibração é uma ferramenta essencial para garantir que os produtos sejam seguros e confiáveis.
Além disso, a calibração dimensional promove a melhoria contínua dos processos de produção. Ao monitorar e calibrar regularmente os instrumentos de medição, as empresas podem identificar áreas de melhoria e implementar mudanças que resultem em produtos de maior qualidade. A calibração não é apenas uma atividade reativa, mas também uma oportunidade para as empresas se tornarem proativas em relação à qualidade. Isso se alinha com os princípios de melhoria contínua, que são fundamentais para o sucesso a longo prazo em um ambiente competitivo.
Por fim, a calibração dimensional contribui para a satisfação do cliente. Quando os produtos atendem ou superam as expectativas dos clientes em termos de qualidade e desempenho, a satisfação do cliente aumenta. A calibração regular dos instrumentos de medição é uma parte fundamental desse processo, pois garante que os produtos sejam fabricados com precisão e consistência. Clientes satisfeitos são mais propensos a se tornar clientes fiéis e a recomendar a empresa a outros, o que pode resultar em um aumento nas vendas e na participação de mercado.
Em resumo, os benefícios da calibração dimensional para a qualidade do produto incluem a redução de erros de medição, a conformidade com normas e regulamentos, a eficiência operacional, a valorização do produto, a segurança do produto, a promoção da melhoria contínua e a satisfação do cliente. Investir em calibração dimensional é uma estratégia inteligente para garantir a qualidade e a competitividade no mercado. As empresas que priorizam a calibração e a precisão nas medições estão melhor posicionadas para atender às demandas do mercado e conquistar a confiança dos clientes.
6. Erros Comuns na Calibração Dimensional e Como Evitá-los
A calibração dimensional é um processo crítico para garantir a precisão e a confiabilidade dos instrumentos de medição utilizados na indústria. No entanto, existem erros comuns que podem ocorrer durante esse processo, comprometendo a qualidade das medições e, consequentemente, a qualidade do produto final. Neste artigo, abordaremos os erros mais frequentes na calibração dimensional e forneceremos orientações sobre como evitá-los.
Um dos erros mais comuns na calibração dimensional é a falta de preparação do ambiente. A calibração deve ser realizada em um ambiente controlado, onde as condições de temperatura, umidade e vibração sejam monitoradas. Se o ambiente não for adequado, as medições podem ser afetadas, resultando em resultados imprecisos. Para evitar esse erro, é fundamental garantir que o local de calibração esteja limpo, livre de contaminantes e que as condições ambientais estejam dentro dos limites especificados. Realizar a calibração em um ambiente controlado é essencial para obter resultados confiáveis.
Outro erro frequente é a utilização de padrões de referência inadequados. Os padrões de referência utilizados na calibração devem ser certificados e reconhecidos, garantindo que suas medições sejam válidas. Se forem utilizados padrões de baixa qualidade ou não calibrados, os resultados da calibração podem ser comprometidos. Para evitar esse erro, é importante verificar a certificação dos padrões de referência e garantir que eles estejam dentro do prazo de validade. Além disso, os padrões devem ser armazenados e manuseados adequadamente para evitar danos.
A falta de treinamento adequado dos profissionais responsáveis pela calibração é outro erro comum. A calibração dimensional requer conhecimento técnico e habilidades específicas. Profissionais não treinados podem cometer erros durante o processo, resultando em medições imprecisas. Para evitar esse problema, as empresas devem investir em treinamento e capacitação para seus funcionários. Isso inclui não apenas o treinamento inicial, mas também a atualização contínua sobre as melhores práticas e novas tecnologias de calibração.
Além disso, a documentação inadequada dos resultados da calibração pode levar a erros. A documentação é uma parte crucial do processo de calibração, pois fornece um registro das medições realizadas e dos ajustes feitos. Se a documentação não for feita corretamente, pode ser difícil rastrear problemas ou verificar a conformidade com as normas de qualidade. Para evitar esse erro, é importante estabelecer um sistema de documentação claro e consistente, garantindo que todas as informações relevantes sejam registradas de forma precisa e acessível.
Outro erro comum é a realização de calibrações irregulares. A calibração não deve ser vista como uma atividade única, mas sim como parte de um programa contínuo de manutenção e controle de qualidade. Se as calibrações forem realizadas de forma irregular, os instrumentos podem se tornar imprecisos ao longo do tempo. Para evitar esse problema, as empresas devem estabelecer um cronograma de calibração regular com base nas recomendações do fabricante e nas normas de qualidade aplicáveis. Manter um cronograma adequado ajuda a garantir que os instrumentos permaneçam precisos e confiáveis.
A negligência na verificação pós-calibração também é um erro que pode comprometer a qualidade das medições. Após a calibração, é fundamental realizar testes de verificação para garantir que o instrumento esteja operando dentro das especificações. Se essa verificação não for realizada, pode haver a possibilidade de que o instrumento ainda apresente desvios. Para evitar esse erro, as empresas devem incluir a verificação pós-calibração como parte do processo padrão de calibração, garantindo que todos os instrumentos sejam testados antes de serem colocados de volta em uso.
Além disso, a falta de manutenção dos instrumentos de medição pode levar a erros na calibração. Instrumentos que não são mantidos adequadamente podem apresentar desgastes ou danos que afetam suas medições. Para evitar esse problema, é importante implementar um programa de manutenção regular para todos os instrumentos de medição. Isso inclui limpeza, lubrificação e inspeções visuais para identificar possíveis problemas antes que eles se tornem críticos.
Por fim, a subestimação da importância da calibração pode levar a erros significativos. Algumas empresas podem considerar a calibração como uma tarefa secundária ou desnecessária, o que pode resultar em medições imprecisas e produtos de baixa qualidade. Para evitar esse erro, é fundamental que as empresas reconheçam a importância da calibração dimensional e a integrem em sua estratégia de gestão da qualidade. Investir em calibração não é apenas uma questão de conformidade, mas uma estratégia inteligente para melhorar a qualidade e a competitividade no mercado.
Em resumo, os erros comuns na calibração dimensional incluem a falta de preparação do ambiente, a utilização de padrões de referência inadequados, a falta de treinamento adequado, a documentação inadequada, a realização de calibrações irregulares, a negligência na verificação pós-calibração, a falta de manutenção dos instrumentos e a subestimação da importância da calibração. Ao estar ciente desses erros e implementar medidas para evitá-los, as empresas podem garantir que seus processos de calibração sejam eficazes e que seus instrumentos de medição permaneçam precisos e confiáveis. Isso, por sua vez, contribui para a qualidade do produto e a satisfação do cliente.
A calibração dimensional é, sem dúvida, um pilar essencial para a qualidade e a eficiência na indústria. Ao garantir que os instrumentos de medição estejam sempre precisos e confiáveis, as empresas não apenas atendem às exigências de qualidade, mas também fortalecem sua posição no mercado. A compreensão dos métodos de calibração, a identificação de erros comuns e a implementação de práticas adequadas são passos cruciais para otimizar processos e garantir a satisfação do cliente. Investir em calibração dimensional é, portanto, uma estratégia inteligente que resulta em produtos de alta qualidade, maior eficiência operacional e, consequentemente, na fidelização dos clientes. Com um compromisso contínuo com a calibração e a melhoria, as empresas podem se destacar em um ambiente competitivo e em constante evolução.