Calibração de Instrumentos Industriais para Garantir Precisão e Confiabilidade
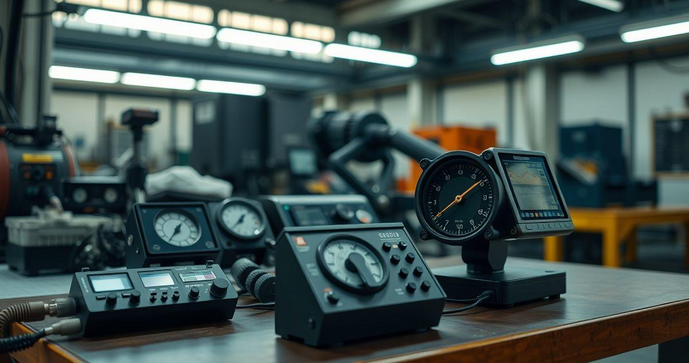
Por: Mauricio - 24 de Janeiro de 2025
A calibração de instrumentos industriais é um processo fundamental para garantir a precisão e a confiabilidade das medições em ambientes de produção. Com a crescente demanda por qualidade e eficiência, a calibração adequada se torna essencial para evitar erros que podem comprometer a segurança e a eficácia dos processos. Neste artigo, abordaremos a importância da calibração, os métodos utilizados, a frequência recomendada e os erros comuns que devem ser evitados.
Importância da Calibração de Instrumentos Industriais
A calibração de instrumentos industriais é um aspecto crucial para a manutenção da qualidade e da precisão em processos produtivos. Este procedimento envolve a comparação das medições de um instrumento com padrões conhecidos e estabelecidos, garantindo que os resultados obtidos estejam dentro das especificações exigidas. A seguir, discutiremos as principais razões pelas quais a calibração é vital para o setor industrial.
Primeiramente, a calibração assegura a precisão das medições. Em ambientes industriais, instrumentos como manômetros, termômetros, balanças e medidores de pressão são utilizados para monitorar e controlar processos. Se esses instrumentos não estiverem calibrados corretamente, as medições podem ser imprecisas, levando a decisões erradas que podem afetar a qualidade do produto final. Por exemplo, um termômetro que não está calibrado pode indicar uma temperatura incorreta, resultando em processos de aquecimento ou resfriamento inadequados, o que pode comprometer a integridade do produto.
Além disso, a calibração é essencial para a conformidade com normas e regulamentos. Muitas indústrias operam sob rigorosos padrões de qualidade, como ISO 9001, que exigem que os instrumentos de medição sejam calibrados regularmente. A não conformidade com essas normas pode resultar em penalidades, perda de certificações e até mesmo a interrupção das operações. Portanto, manter um programa de calibração eficaz é fundamental para garantir que a empresa esteja em conformidade com as exigências legais e de mercado.
Outro ponto importante é a redução de custos. Instrumentos não calibrados podem levar a erros de medição que, por sua vez, podem resultar em desperdício de materiais, retrabalho e até mesmo falhas de produção. Por exemplo, se uma balança não estiver calibrada corretamente, pode resultar em quantidades erradas de matéria-prima sendo utilizadas, levando a um aumento nos custos de produção. Ao investir na calibração regular dos instrumentos, as empresas podem evitar esses custos adicionais e melhorar a eficiência operacional.
A calibração também contribui para a segurança no ambiente de trabalho. Instrumentos de medição são frequentemente utilizados para monitorar condições críticas, como pressão e temperatura, que podem impactar a segurança dos trabalhadores e das instalações. Um instrumento que não está calibrado pode não detectar condições perigosas, colocando em risco a segurança dos funcionários e a integridade das instalações. Portanto, garantir que os instrumentos estejam calibrados é uma medida preventiva essencial para evitar acidentes e garantir um ambiente de trabalho seguro.
Além disso, a calibração ajuda a aumentar a confiança dos clientes. Quando uma empresa demonstra que seus instrumentos de medição são calibrados e mantidos de acordo com padrões rigorosos, isso transmite uma imagem de qualidade e confiabilidade. Os clientes tendem a confiar mais em produtos que são fabricados por empresas que seguem práticas de calibração adequadas, o que pode resultar em maior satisfação do cliente e fidelização.
Outro aspecto a ser considerado é a melhoria contínua dos processos. A calibração não é apenas uma atividade pontual, mas parte de um ciclo de melhoria contínua. Ao monitorar e calibrar regularmente os instrumentos, as empresas podem identificar tendências e variações nas medições, permitindo ajustes proativos nos processos. Isso não apenas melhora a qualidade do produto, mas também pode levar a inovações e melhorias operacionais.
Por fim, é importante ressaltar que a calibração deve ser realizada por profissionais qualificados e em empresas especializadas. A escolha de uma Empresa de calibração confiável é fundamental para garantir que os instrumentos sejam calibrados de acordo com os padrões corretos e que os resultados sejam precisos. Profissionais experientes têm o conhecimento e as ferramentas necessárias para realizar calibrações de forma eficaz, garantindo que os instrumentos estejam sempre prontos para uso.
Em resumo, a calibração de instrumentos industriais é uma prática indispensável que impacta diretamente a precisão, a conformidade, a segurança e a eficiência operacional das empresas. Investir em um programa de calibração robusto não apenas melhora a qualidade dos produtos, mas também fortalece a reputação da empresa no mercado. Portanto, é essencial que as indústrias reconheçam a importância da calibração e implementem práticas adequadas para garantir o sucesso a longo prazo.
Métodos Comuns de Calibração
A calibração de instrumentos é um processo essencial para garantir a precisão e a confiabilidade das medições em ambientes industriais. Existem diversos métodos de calibração que podem ser aplicados, dependendo do tipo de instrumento, da aplicação e dos requisitos específicos de cada setor. Neste artigo, abordaremos alguns dos métodos mais comuns de calibração, suas características e quando utilizá-los.
Um dos métodos mais tradicionais de calibração é a calibração por comparação. Este método envolve a comparação das medições de um instrumento com um padrão de referência conhecido e rastreável. O instrumento a ser calibrado é colocado em operação ao lado de um instrumento de referência que já foi calibrado e verificado. As medições são então comparadas, e qualquer desvio é registrado. Este método é amplamente utilizado para instrumentos de medição de pressão, temperatura e fluxo, pois permite identificar rapidamente qualquer erro de medição. A calibração por comparação é eficaz, mas requer que o instrumento de referência esteja sempre disponível e em boas condições.
Outro método comum é a calibração por ajuste. Neste caso, o instrumento é ajustado para que suas medições correspondam aos valores de um padrão de referência. Este método é frequentemente utilizado em instrumentos que possuem um mecanismo de ajuste interno, como balanças e termômetros. Durante o processo de calibração, o técnico ajusta o instrumento até que as medições estejam dentro das especificações desejadas. A calibração por ajuste é útil quando o instrumento apresenta desvios sistemáticos que podem ser corrigidos, garantindo que ele funcione corretamente em futuras medições.
A calibração por simulação é um método que utiliza um dispositivo de simulação para gerar sinais de entrada que imitam as condições reais de operação do instrumento. Este método é especialmente útil para instrumentos eletrônicos, como multímetros e osciloscópios. Durante a calibração, o dispositivo de simulação é conectado ao instrumento, e diferentes valores de entrada são aplicados. O técnico verifica se as saídas do instrumento correspondem aos valores esperados. A calibração por simulação é eficaz para identificar problemas de linearidade e resposta do instrumento, além de ser uma abordagem prática para calibrações em campo.
Outro método importante é a calibração por transferência. Este método é utilizado quando não é possível realizar a calibração diretamente no instrumento a ser verificado. Em vez disso, um instrumento de referência é calibrado em um laboratório e, em seguida, transportado para o local onde o instrumento a ser calibrado está instalado. O instrumento de referência é utilizado para realizar medições no instrumento em questão, permitindo a comparação e a verificação da precisão. A calibração por transferência é comum em ambientes onde o acesso ao laboratório de calibração é limitado, mas ainda é necessário garantir a precisão das medições.
A calibração em laboratório é outro método amplamente utilizado, especialmente para instrumentos que exigem condições controladas. Neste caso, os instrumentos são enviados para um laboratório especializado, onde são calibrados por técnicos qualificados. O laboratório utiliza padrões de referência rastreáveis e equipamentos de alta precisão para garantir que as medições estejam dentro das especificações. A calibração em laboratório é ideal para instrumentos que não podem ser calibrados no local de operação ou que exigem um ambiente controlado para garantir resultados precisos.
Além dos métodos mencionados, a calibração por ponto fixo é uma técnica que envolve a verificação de um instrumento em pontos específicos de sua faixa de medição. Este método é útil para instrumentos que não precisam ser calibrados em toda a sua faixa, mas apenas em pontos críticos. Por exemplo, um termômetro pode ser calibrado em pontos de congelamento e ebulição da água, garantindo que as medições nessas temperaturas sejam precisas. A calibração por ponto fixo é uma abordagem eficiente que economiza tempo e recursos, focando apenas nas áreas mais relevantes para a aplicação.
Por fim, é importante ressaltar que a escolha do método de calibração deve ser baseada nas necessidades específicas de cada instrumento e nas exigências do setor. Para garantir a eficácia do processo de calibração, é recomendável contar com uma Empresa de calibração de equipamentos especializada, que possa fornecer suporte técnico e garantir que os instrumentos sejam calibrados de acordo com os padrões adequados.
Em resumo, os métodos de calibração variam de acordo com o tipo de instrumento e as necessidades específicas de cada aplicação. A calibração por comparação, ajuste, simulação, transferência, laboratório e ponto fixo são algumas das abordagens mais comuns utilizadas na indústria. Cada método tem suas vantagens e desvantagens, e a escolha do mais adequado depende das circunstâncias e dos requisitos de precisão. Ao implementar um programa de calibração eficaz, as empresas podem garantir a qualidade e a confiabilidade de suas medições, contribuindo para a eficiência e a segurança de seus processos produtivos.
Frequência Recomendada para Calibração
A calibração de instrumentos é uma prática essencial para garantir a precisão e a confiabilidade das medições em ambientes industriais. No entanto, a eficácia desse processo depende não apenas da qualidade da calibração em si, mas também da frequência com que ela é realizada. Neste artigo, discutiremos a frequência recomendada para calibração, fatores que influenciam essa frequência e a importância de manter um cronograma adequado.
A frequência de calibração pode variar significativamente de acordo com o tipo de instrumento, a aplicação, o ambiente de operação e as exigências regulatórias. Em geral, muitos fabricantes de instrumentos recomendam que a calibração seja realizada anualmente. No entanto, essa é uma diretriz geral e pode não se aplicar a todas as situações. Por exemplo, instrumentos utilizados em ambientes críticos, como laboratórios de pesquisa ou indústrias farmacêuticas, podem exigir calibrações mais frequentes, como a cada seis meses ou até trimestralmente. Isso se deve à necessidade de garantir medições extremamente precisas e confiáveis, que são essenciais para a segurança e a eficácia dos produtos.
Outro fator a ser considerado é a intensidade de uso do instrumento. Instrumentos que são utilizados com frequência ou que estão sujeitos a condições adversas, como vibrações, temperaturas extremas ou umidade, podem precisar de calibrações mais frequentes. Por exemplo, um manômetro utilizado em um ambiente industrial com altas vibrações pode sofrer desgastes mais rapidamente, exigindo uma calibração mais regular para garantir que suas medições permaneçam precisas. Portanto, é importante avaliar o ambiente de operação e a carga de trabalho do instrumento ao determinar a frequência de calibração.
Além disso, a natureza do processo em que o instrumento está inserido também influencia a frequência de calibração. Em processos críticos, onde pequenas variações nas medições podem resultar em grandes impactos na qualidade do produto ou na segurança, a calibração deve ser realizada com mais frequência. Por exemplo, em indústrias alimentícias, onde a precisão nas medições de temperatura e umidade é crucial para garantir a segurança dos produtos, a calibração pode ser necessária a cada lote produzido. Isso ajuda a evitar problemas de qualidade e a garantir que os produtos atendam aos padrões de segurança.
As exigências regulatórias também desempenham um papel importante na determinação da frequência de calibração. Muitas indústrias operam sob normas rigorosas que exigem calibrações regulares para garantir a conformidade com os padrões de qualidade e segurança. Por exemplo, a norma ISO 9001 estabelece diretrizes para a calibração de instrumentos, e as empresas que buscam certificação devem seguir essas diretrizes. Portanto, é fundamental que as empresas estejam cientes das regulamentações aplicáveis ao seu setor e ajustem suas práticas de calibração de acordo.
Além disso, a implementação de um programa de manutenção preventiva pode ajudar a otimizar a frequência de calibração. Ao realizar inspeções regulares e manutenções nos instrumentos, as empresas podem identificar problemas antes que eles afetem a precisão das medições. Isso pode permitir que a frequência de calibração seja ajustada com base nas condições reais de operação, em vez de seguir um cronograma fixo. Um programa de manutenção preventiva bem estruturado pode, portanto, contribuir para a eficiência operacional e a redução de custos.
É importante ressaltar que a calibração não deve ser vista apenas como uma tarefa a ser realizada em intervalos regulares, mas sim como parte de um ciclo contínuo de melhoria. A análise dos resultados das calibrações anteriores pode fornecer informações valiosas sobre o desempenho dos instrumentos e ajudar a identificar tendências que podem indicar a necessidade de ajustes na frequência de calibração. Por exemplo, se um instrumento apresenta desvios frequentes em suas medições, pode ser necessário aumentar a frequência de calibração para garantir que ele permaneça dentro das especificações.
Para garantir a eficácia do processo de calibração, é recomendável contar com um Serviço de calibração especializado. Profissionais qualificados têm o conhecimento e a experiência necessários para realizar calibrações de forma eficaz, garantindo que os instrumentos estejam sempre prontos para uso. Além disso, eles podem ajudar a estabelecer um cronograma de calibração adequado com base nas necessidades específicas de cada instrumento e nas exigências do setor.
Em resumo, a frequência recomendada para calibração varia de acordo com diversos fatores, incluindo o tipo de instrumento, a intensidade de uso, a natureza do processo e as exigências regulatórias. Embora a calibração anual seja uma diretriz comum, muitas situações podem exigir calibrações mais frequentes. A implementação de um programa de manutenção preventiva e a análise contínua dos resultados das calibrações podem ajudar a otimizar a frequência de calibração e garantir a precisão e a confiabilidade das medições. Ao manter um cronograma adequado de calibração, as empresas podem melhorar a qualidade de seus produtos, garantir a segurança de seus processos e atender às exigências regulatórias de forma eficaz.
Erros Comuns na Calibração e Como Evitá-los
A calibração de instrumentos é um processo crítico para garantir a precisão e a confiabilidade das medições em ambientes industriais. No entanto, existem diversos erros que podem ocorrer durante esse processo, comprometendo a eficácia da calibração e, consequentemente, a qualidade dos produtos e a segurança dos processos. Neste artigo, abordaremos os erros comuns na calibração e como evitá-los, garantindo que os instrumentos funcionem de maneira adequada.
Um dos erros mais frequentes na calibração é a falta de um padrão de referência adequado. A calibração deve ser realizada em comparação com padrões de referência que sejam rastreáveis e reconhecidos. Se o padrão utilizado não for adequado ou não estiver calibrado, as medições do instrumento a ser calibrado também estarão incorretas. Para evitar esse erro, é fundamental utilizar padrões de referência que sejam certificados e que atendam às normas aplicáveis. Além disso, é importante garantir que esses padrões sejam recalibrados regularmente para manter sua precisão.
Outro erro comum é a falta de condições ambientais controladas durante o processo de calibração. A temperatura, a umidade e a pressão atmosférica podem afetar significativamente as medições dos instrumentos. Se a calibração for realizada em um ambiente com condições variáveis, os resultados podem ser imprecisos. Para evitar esse problema, é recomendável realizar a calibração em um ambiente controlado, onde as condições possam ser monitoradas e mantidas dentro de limites aceitáveis. Isso é especialmente importante para instrumentos sensíveis, como balanças e termômetros.
A calibração inadequada do instrumento também é um erro que pode ocorrer. Isso pode acontecer quando o técnico responsável pela calibração não possui o conhecimento ou a experiência necessária para realizar o procedimento corretamente. A falta de treinamento adequado pode levar a erros na configuração do instrumento, na aplicação dos padrões de referência ou na interpretação dos resultados. Para evitar esse erro, é essencial que os técnicos que realizam a calibração sejam devidamente treinados e qualificados. Investir em capacitação e atualização profissional é fundamental para garantir a qualidade do processo de calibração.
Além disso, a falta de documentação adequada é um erro que pode comprometer a rastreabilidade e a confiabilidade dos resultados da calibração. É importante registrar todos os detalhes do processo de calibração, incluindo os padrões utilizados, as condições ambientais, os resultados obtidos e quaisquer ajustes realizados. A documentação adequada não apenas ajuda a garantir a conformidade com as normas, mas também fornece um histórico que pode ser útil para futuras calibrações e auditorias. Para evitar esse erro, as empresas devem implementar um sistema de gerenciamento de documentos que facilite o registro e o armazenamento das informações de calibração.
Outro erro comum é a calibração em intervalos inadequados. A frequência de calibração deve ser determinada com base nas necessidades específicas de cada instrumento e nas exigências do setor. Calibrar um instrumento com muita frequência pode resultar em custos desnecessários, enquanto calibrá-lo com pouca frequência pode comprometer a precisão das medições. Para evitar esse erro, é importante estabelecer um cronograma de calibração que leve em consideração fatores como a intensidade de uso, as condições de operação e as exigências regulatórias. Revisar e ajustar esse cronograma regularmente pode ajudar a garantir que os instrumentos sejam calibrados de maneira adequada.
A falta de verificação pós-calibração é outro erro que pode ocorrer. Após a calibração, é fundamental realizar testes para garantir que o instrumento esteja funcionando corretamente e que as medições estejam dentro das especificações. Ignorar essa etapa pode resultar em instrumentos que parecem estar calibrados, mas que ainda apresentam desvios em suas medições. Para evitar esse erro, as empresas devem implementar um procedimento de verificação pós-calibração que inclua testes de desempenho e comparação com padrões de referência.
Por fim, a escolha inadequada de uma Empresa de calibração de instrumentos de medição pode levar a erros na calibração. É fundamental selecionar uma empresa que possua a experiência, as certificações e os recursos necessários para realizar calibrações de forma eficaz. A falta de credibilidade da empresa pode resultar em calibrações imprecisas e em instrumentos que não atendem aos padrões exigidos. Para evitar esse erro, as empresas devem realizar uma pesquisa cuidadosa ao escolher um prestador de serviços de calibração, verificando suas credenciais e referências.
Em resumo, os erros comuns na calibração podem comprometer a precisão e a confiabilidade das medições, afetando a qualidade dos produtos e a segurança dos processos. Para evitar esses erros, é fundamental utilizar padrões de referência adequados, realizar a calibração em condições ambientais controladas, garantir que os técnicos sejam qualificados, manter documentação adequada, calibrar os instrumentos em intervalos apropriados, realizar verificações pós-calibração e escolher uma empresa de calibração confiável. Ao implementar essas práticas, as empresas podem garantir que seus instrumentos estejam sempre prontos para fornecer medições precisas e confiáveis.
Em conclusão, a calibração de instrumentos industriais é uma prática indispensável que impacta diretamente a qualidade e a segurança dos processos produtivos. Através da compreensão da importância da calibração, dos métodos adequados, da frequência recomendada e dos erros comuns a serem evitados, as empresas podem estabelecer um sistema robusto de controle de qualidade. Investir em calibração não apenas assegura medições precisas, mas também fortalece a confiança dos clientes e a conformidade com normas regulatórias. Portanto, é essencial que as indústrias adotem práticas de calibração eficazes e mantenham um compromisso contínuo com a melhoria da qualidade em suas operações.