Calibração de Instrumentos Industriais: O que Você Precisa Saber
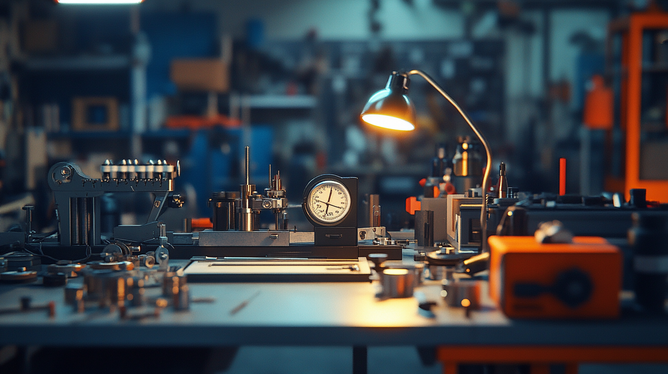
Por: Mauricio - 17 de Outubro de 2024
A calibração de instrumentos industriais é um processo fundamental para garantir a precisão e a confiabilidade nas medições utilizadas em diversas atividades. Nesse artigo, você irá aprender sobre a importância da calibração, os métodos utilizados na indústria, os desafios que podem surgir durante esse processo e como manter seus instrumentos devidamente calibrados. Continue lendo e descubra como essa prática pode impactar diretamente a qualidade e segurança dos seus processos industriais.
Importância da Calibração de Instrumentos Industriais
A calibração de instrumentos industriais desempenha um papel crucial em diversas áreas, desde a produção até a segurança. Manter a precisão das medições é essencial para garantir a qualidade dos produtos, a conformidade com normas regulatórias e a eficiência operacional. Neste segmento, abordaremos por que a calibração é tão importante, as consequências da falta de calibração e como ela impacta positivamente as operações industriais.
Garantia da Qualidade do Produto
Um dos principais motivos para realizar a calibração de instrumentos industriais é garantir a qualidade do produto final. Quando os equipamentos de medição não estão calibrados corretamente, as medições podem ser imprecisas, levando à produção de itens defeituosos. Em indústrias como a farmacêutica, alimentícia e de automação, isso pode resultar em produtos que não atendem aos padrões de qualidade e segurança, colocando em risco não apenas a reputação da empresa, mas também a saúde dos consumidores.
Conformidade com Normas e Regulamentações
A calibração também é fundamental para garantir que as empresas estejam em conformidade com normas e regulamentações estabelecidas por órgãos reguladores. Muitos setores possuem requisitos rigorosos sobre a precisão das medições, e a falta de calibração pode resultar em sanções, multas e até mesmo na interrupção das operações. Além disso, a calibração regular é frequentemente uma exigência para obter certificações de qualidade, como ISO 9001, que garantem processos eficientes e produtos confiáveis.
Redução de Custos
Embora a calibração exija um investimento inicial, ela pode levar a uma redução significativa de custos a longo prazo. Quando instrumentos não calibrados são usados, aumenta-se o risco de falhas e retrabalho, gerando desperdício de materiais e tempo. Calibrar os instrumentos regularmente ajuda a identificar problemas antes que se tornem críticos, permitindo ações corretivas que previnem paradas inesperadas e reparos dispendiosos.
Aumento da Eficiência Operacional
A calibração de instrumentos industriais também está diretamente relacionada ao aumento da eficiência operacional. Equipamentos calibrados permitem medições mais precisas, o que, por sua vez, resulta em um processo de produção mais eficiente. Isso significa que as máquinas podem operar em suas capacidades máximas, minimizando o tempo de inatividade e aumentando a produção. Além disso, a precisão das medições contribui para otimizações nos processos, como o ajuste de parâmetros para maximizar a qualidade do produto.
Segurança no Ambiente de Trabalho
A calibração adequada é uma questão de segurança, especialmente em indústrias que lidam com produtos químicos, eletricidade ou equipamentos pesados. Instrumentos não calibrados podem levar a medições incorretas, resultando em acidentes que podem ferir funcionários e causar danos materiais significativos. Por exemplo, em uma planta química, medidores de pressão e temperatura com leitura errada podem gerar explosões ou vazamentos tóxicos. Portanto, a calibração não é apenas uma exigência operacional, mas uma necessidade de segurança.
Confiança e Satisfação do Cliente
Calibrar os instrumentos industriais ajuda a garantir a precisão e a confiabilidade dos produtos, o que, por sua vez, leva à confiança do cliente. Quando as empresas mantêm padrões elevados de qualidade por meio de calibração rigorosa, os clientes tendem a permanecer leais à marca. Em um mercado competitivo, essa reputação pode ser um diferencial crítico. Clientes satisfeitos são mais propensos a recomendar a empresa e fazer novas compras, contribuindo para o crescimento sustentável do negócio.
Métodos de Calibração e Tecnologias
A calibração de instrumentos pode ser realizada através de diversos métodos e tecnologias, dependendo do tipo de equipamento utilizado e das especificações do processo. Os métodos mais comuns incluem calibração pontual, calibração em laboratório e calibração em campo. Cada um desses métodos tem suas características únicas, e a escolha do método deve ser baseada nas necessidades específicas da indústria e dos instrumentos.
Na calibração pontual, o instrumento é testado em um determinado ponto de operação e comparado com um padrão de referência. Já na calibração em laboratório, os instrumentos são levados a um ambiente controlado, onde são submetidos a uma série de testes para verificar sua precisão. A calibração em campo é realizada no local de operação e pode incluir diagnósticos em tempo real, permitindo ajustes imediatos.
Frequência de Calibração
Determinar a frequência adequada para a calibração é outra parte importante do processo. Fatores como o tipo de instrumento, as condições de operação e a frequência de uso devem ser considerados. Em geral, instrumentos que são usados em ambientes extremos ou que enfrentam desgaste regular devem ser calibrados com mais frequência. Além disso, integridade assegurada requer que a calibração ocorra antes e após eventos significativos, como a manutenção ou a substituição de peças.
Documentação e Registros de Calibração
A documentação é um aspecto vital na calibração de instrumentos industriais. Registros detalhados ajudam a comprovar que a calibração foi realizada adequadamente e que todos os procedimentos foram seguidos. Manter um histórico de calibração é essencial para auditorias e revisões de conformidade. Esses registros também permitem que as empresas analisem tendências e identifiquem áreas de melhoria ao longo do tempo.
Documentar a calibração geralmente envolve a criação de um relatório que inclui informações como data, instrumentos calibrados, resultados dos testes, ajustes realizados e a assinatura do responsável. Essa documentação deve ser armazenada de maneira acessível e organizada para que possa ser facilmente consultada quando necessário.
Implementação de um Plano de Calibração
Para garantir que a calibração seja realizada de forma eficaz, as empresas devem implementar um plano de calibração abrangente. Esse plano deve incluir a identificação de instrumentos a serem calibrados, a frequência das calibrações, os métodos utilizados, a documentação e a formação da equipe. Ao ter uma abordagem sistemática para a calibração, as empresas podem garantir que todos os aspectos sejam considerados e geridos de maneira eficaz.
Uma comunicação clara é necessária entre as equipes envolvidas para garantir que todos estejam cientes de suas responsabilidades em relação à calibração. Além disso, a realização de verificações regulares e auditorias do plano de calibração pode ajudar a identificar áreas de melhoria e garantir a conformidade.Ao focar na calibração de instrumentos industriais, as empresas não apenas asseguram a precisão nas medições, mas também criam um ambiente de trabalho mais seguro e eficiente. A calibração deve ser vista como uma parte essencial da estratégia operacional, em vez de uma tarefa secundária. Assim, as empresas podem se posicionar como líderes em qualidade e inovação em suas respectivas indústrias.
A calibração de instrumentos industriais é uma prática essencial que traz benefícios diretos e significativos para as operações. Ao compreender a importância e adotar os melhores métodos, as indústrias podem maximizar a eficiência e garantir a qualidade e segurança de seus produtos. Quando feita de forma consistente, a calibração fortalece a base sobre a qual as operações industriais são construídas, gerando resultados duradouros e confiança no mercado.
Métodos de Calibração Usados na Indústria
A calibração de instrumentos industriais é uma prática essencial que garante a precisão e a confiabilidade nas medições. Os métodos de calibração utilizados podem variar dependendo do tipo de instrumento, do setor industrial e das necessidades específicas de cada processo. Neste segmento, abordaremos os métodos mais comuns de calibração usados na indústria, suas aplicações, vantagens e desvantagens, bem como as melhores práticas para implementá-los.
Calibração em Laboratório
A calibração em laboratório é um dos métodos mais precisos e controlados disponíveis. Neste método, os instrumentos são retirados do local de operação e enviados a um laboratório especializado, onde passam por uma série de testes para avaliar sua precisão em comparação com padrões de referência. Os laboratórios costumam ter condições controladas, o que ajuda a minimizar a interferência de fatores externos nas medições.
As principais vantagens da calibração em laboratório incluem:
- Precisão Elevada: Devido ao ambiente controlado, os resultados das medições são mais confiáveis.
- Equipamentos Avançados: Laboratórios geralmente possuem equipamentos de calibração de última geração, proporcionando um nível maior de precisão.
- Registros Documentados: A maioria dos laboratórios emite certificados de calibração que documentam os resultados, indispensáveis para auditorias e conformidade regulatória.
No entanto, esse método também apresenta desvantagens:
- Interrupção de Operações: Retirar instrumentos da linha de produção pode causar atrasos e interrupções.
- Custos Adicionais: O transporte de instrumentos até o laboratório pode gerar custos adicionais.
- Limitação de Instrumentos: Nem todos os instrumentos podem ser facilmente transportados, especialmente aqueles que são volumosos ou pesados.
Calibração em Campo
A calibração em campo, por outro lado, é realizada diretamente no local onde os instrumentos estão sendo utilizados. Esse método é ideal para instrumentos que são grandes, pesados ou críticos para as operações, pois não requer transporte. Também é útil quando a calibração precisa ser feita rapidamente para evitar longos períodos de inatividade.
As vantagens da calibração em campo incluem:
- Minimização do Tempo de Inatividade: A calibração ocorre no local, permitindo que as operações continuem com interrupções mínimas.
- Immediate Feedback: Os ajustes necessários podem ser feitos imediatamente, garantindo que os instrumentos estejam prontos para o uso rápido.
- Custo-Benefício: Reduz custos associados ao transporte e ao tempo necessário para a calibração em laboratório.
As desvantagens do método em campo podem incluir:
- Ambiente Não Controlado: Fatores como temperatura, umidade e vibrações podem interferir nos resultados.
- Menos Precisão: Em comparação com a calibração em laboratório, a precisão pode ser menor devido às condições variáveis do ambiente.
- Necessidade de Especialização: Requer técnicos altamente qualificados para calibrar instrumentos de forma eficaz.
Calibração Comparativa
A calibração comparativa é um método onde um instrumento não calibrado é comparado com um padrão de referência conhecido e já calibrado, permitindo determinar se o primeiro está funcionando corretamente. Essa abordagem é muitas vezes usada para instrumentos que não têm um método de calibração direta disponível.
Vantagens da calibração comparativa incluem:
- Flexibilidade: Pode ser aplicada a uma ampla variedade de instrumentos e aplicações.
- Menor Custo: Geralmente, menos custosa do que calibrações diretas, uma vez que exige menos recursos.
- Rápido e Eficiente: A calibração pode ser realizada rapidamente, aumentando a eficiência operacional.
Entretanto, suas desvantagens são:
- Dependência de Padrões: A precisão depende da qualidade e confiabilidade do padrão de referência utilizado.
- Limitações de Resultado: Embora forneça uma visão geral da precisão, pode não identificar desvios específicos nas medições do instrumento.
Calibração Ponto a Ponto
A calibração ponto a ponto, ou calibração de nível único, envolve testar as medições em um ou mais pontos específicos ao longo do intervalo do instrumento. Esse método é comumente utilizado quando o instrumento apresenta características lineares, permitindo que os técnicos identifiquem desvios em medições específicas.
As vantagens incluem:
- Simples e Direto: Fácil de executar, especialmente para instrumentos com resposta linear.
- Identificação de Pontos Críticos: Permite que os técnicos identifiquem rapidamente falhas em medições específicas.
- Custo-Benefício: Geralmente, mais econômico do que calibrações completas ao longo de todo o intervalo.
Por outro lado, suas desvantagens incluem:
- Visualização Limitada: Não fornece uma visão completa do desempenho em todo o intervalo de medição.
- Risco de Ignorar Erros: Pode perder erros fora dos pontos testados.
Calibração Automática
Nos últimos anos, a calibração automática tem ganhado popularidade, especialmente em ambientes industrializados e altamente automatizados. Esse método utiliza sistemas computadorizados para realizar a calibração sem intervenção humana, com o intuito de aumentar a precisão e a eficiência.
As principais vantagens incluem:
- Consistência: As calibrações são realizadas de forma consistente, reduzindo a margem de erro humano.
- Eficiência: O processo pode ser integrado aos ciclos de operação, minimizando o tempo de inatividade.
- Dados em Tempo Real: Coleta e análise de dados em tempo real para um monitoramento contínuo.
As desvantagens da calibração automática incluem:
- Investimento Inicial: Pode exigir um investimento significativo em tecnologia e equipamentos.
- Complexidade: Requer programação e manutenção, o que pode complicar a operação.
Calibração de Rotina
Além dos métodos tradicionals, muitas indústrias estabelecem um sistema de calibração de rotina, que envolve a realização de calibrações em intervalos regulares para garantir a precisão contínua dos instrumentos. Esta abordagem é fundamental para a manutenção da qualidade em ambientes de produção dinâmica.
As vantagens da calibração de rotina incluem:
- Detecção Precoce de Problemas: A calibração regular permite a identificação de problemas antes que se tornem críticos.
- Conformidade Consistente: Mantém os instrumentos sempre dentro dos padrões de conformidade com regulamentações.
- Melhoria Contínua: Promove um ciclo de melhoria contínua nas operações industriais.
Por outro lado, as desvantagens incluem:
- Custo de Manutenção: Os custos de manutenção podem ser altos se as calibrações forem excessivamente frequentes.
- Planejamento Necessário: Requer planejamento cuidadoso para garantir que as calibrações não interfiram nas operações.
Considerações Finais sobre Métodos de Calibração
A escolha do método de calibração deve ser feita com base nas necessidades específicas da indústria, nas características dos instrumentos a serem calibrados e nas regulamentações em vigor. A calibração não deve ser tratada como uma tarefa pontual, mas sim como parte de uma estratégia contínua de manutenção da qualidade e eficiência.
Investir em calibração de instrumentos industriais é garantir um futuro mais seguro e eficiente para as operações. Com a abordagem correta e a metodologia adequada, as indústrias podem assegurar a precisão das medições, mantendo assim a qualidade dos produtos e a segurança operacional. A calibração é, sem dúvida, um aspecto crítico para a sustentabilidade e competitividade das empresas no cenário industrial atual.
Desafios Comuns na Calibração de Instrumentos
A calibração de instrumentos é um componente vital em muitas indústrias, pois garante que as medições sejam precisas e confiáveis. No entanto, esse processo não vem sem seus desafios. Neste segmento, vamos explorar os desafios mais comuns enfrentados durante a calibração de instrumentos, as causas subjacentes desses problemas e as estratégias que podem ser adotadas para superá-los.
Manutenção de Padrões de Referência
Um dos maiores desafios na calibração é garantir a integridade e a precisão dos padrões de referência utilizados. Os instrumentos precisam ser calibrados em relação a padrões confiáveis que, por sua vez, devem ser mantidos em condições ideais. Isso significa que os padrões de referência também precisam passar por calibrações regulares, e a falta de manutenção adequada pode levar a desvios nas medições.
As principais causas desse desafio incluem:
- Ambientes Inadequados: Padrões de referência podem ser afetados por condições como temperatura, umidade e vibração. Manter um ambiente controlado é crucial para a precisão.
- Uso Excessivo: Padrões de referência que são utilizados com frequência podem se desgastar ou se danificar, prejudicando a sua eficácia.
- Falta de Documentação: A ausência de registros históricos de calibração pode dificultar a verificação da precisão dos padrões ao longo do tempo.
Para superar esse desafio, as empresas devem estabelecer rotinas de manutenção rigorosa para seus padrões de referência. Além disso, um ambiente adequado deve ser criado para protegê-los contra influências externas.
Falta de Treinamento Adequado
Outro desafio significativo é a falta de treinamento e conhecimento entre os técnicos responsáveis pela calibração. A calibração eficaz exige habilidades específicas e compreensão das técnicas e instrumentos utilizados. Quando as pessoas envolvidas na calibração não estão devidamente treinadas, o risco de erros aumenta.
Os principais fatores que contribuem para esse problema incluem:
- Alta Rotatividade: A constante troca de funcionários pode causar lacunas no conhecimento e habilidades necessárias para a calibração correta.
- Desinteresse ou Baixa Prioridade: Muitas vezes, a calibração não é vista como uma prioridade, resultando em treinamento inadequado ou abandona de práticas recomendadas.
- Complexidade dos Instrumentos: À medida que a tecnologia avança, os instrumentos tornam-se mais complexos, exigindo treinamento contínuo para os técnicos.
Para resolver esse desafio, as empresas devem implementar programas contínuos de treinamento e certificação para os técnicos de calibração. Além disso, é importante criar uma cultura que valorize a calibração como uma parte crítica do processo operacional.
Variabilidade nas Condições Operacionais
A calibração de instrumentos também é desafiada pela variabilidade das condições operacionais. Fatores como temperatura, pressão, umidade e vibrações podem afetar as medições realizadas pelos instrumentos. Para muitos instrumentos, essa variabilidade pode gerar medições imprecisas, especialmente se os instrumentos não foram projetados para operar em ambientes extremos.
As causas fundamentais desse desafio incluem:
- Localização dos Instrumentos: Instrumentos instalados em áreas industriais podem estar sujeitos a mudanças sazonais ou variabilidades mecânicas que afetam suas medições.
- Integração de Sistemas Físicos e Virtuais: A digitalização de processos pode introduzir complexidades que tornam difícil prever como os instrumentos reagirão em uma variedade de condições.
- Efeitos de Ciclo Térmico: Instrumentos que enfrentam mudanças rápidas de temperatura podem apresentar desvios em suas medições se não forem calibrados corretamente.
Para mitigar esses efeitos, as empresas devem monitorar regularmente as condições operacionais e adaptar os procedimentos de calibração em conformidade. A instalação de sensores ambientais também pode ajudar a prever e compensar a variabilidade.
Resistência à Mudança
Um desafio menos técnico, mas igualmente importante, é a resistência à mudança dentro das organizações. Muitas empresas têm políticas de calibração adequadas que são frequentemente ignoradas. Essa resistência pode se originar de uma falta de entendimento sobre a importância da calibração, a crença de que mudanças não são necessárias ou até mesmo a simples inércia organizacional.
Causas disso incluem:
- Cultura Estabelecida: A tradição e a cultura organizacional podem dificultar a adoção de novas práticas ou tecnologias.
- Custos Percebidos: Alguns funcionários podem ver a calibração como um custo desnecessário, em vez de um investimento em qualidade.
- Falta de Comunicação: A falta de informações claras sobre os benefícios da calibração pode criar desinteresse entre os funcionários.
Superar a resistência à mudança exige um esforço coordenado na comunicação dos benefícios da calibração e a implementação de práticas que incentivem a participação dos funcionários. Workshops e sessões de informação podem ajudar a aumentar a conscientização sobre a importância da calibração.
Identificação de Instrumentos Não Calibráveis
Em algumas situações, pode haver instrumentos que não podem ser calibrados de maneira efetiva, ou que exigem métodos específicos de calibração que não estão disponíveis. Isso pode ser um grande desafio para empresas que necessitam de medições precisas em todos os aspectos de suas operações.
Causas que contribuem para esse problema incluem:
- Instrumentos Antigos: Equipamentos mais antigos podem não ter o suporte necessário para calibração devido à obsolescência.
- Instrumentos Específicos de Nicho: Alguns instrumentos são altamente especializados e podem não ter disponíveis padrões de referência apropriados para a calibração.
- Complexidade da Tecnologia: A complexidade intrínseca de alguns dispositivos pode dificultar a aplicação de métodos padrão de calibração.
Para superar esse desafio, as empresas podem precisar considerar a possibilidade de investir em equipamentos mais novos e modernos, que tenham suporte para calibração eficaz. Além disso, a identificação de fornecedores que oferecem serviços de calibração especializados pode ser uma solução prática.
Registro e Documentação Adequada
A manutenção de registros precisos e adequados é fundamental para o sucesso da calibração, mas muitas empresas enfrentam desafios nesta área. Registros inadequados podem resultar em conformidade insuficiente, dificultando auditorias e a análise de histórico de desempenho dos instrumentos.
As questões que contribuem para a falta de documentação eficaz incluem:
- Processos Manuais: Dependência de papel e processos manuais pode levar a erros e registros incompletos.
- Falta de Padrões: A ausência de padrões para o registro de dados pode resultar na perda de informações críticas.
- Desatualização da Documentação: Registros e certificados podem não ser atualizados após cada calibração, levando a dados desatualizados.
Para melhorar a documentação, as empresas devem implementar sistemas digitais que facilitem a coleta, gestão e armazenamento de dados de calibração. Trabalhadores também devem ser treinados na importância de manter registros precisos e atualizados.
Conformidade com Regulamentações e Normas
A conformidade com regulamentações e normas é um aspecto crítico da calibração, mas muitas indústrias enfrentam desafios para se manter em conformidade com as mudanças frequentes em regulamentações ou setores regulatórios complexos.
As causas deste desafio incluem:
- Normas Variáveis: A falta de uniformidade nas normas entre diferentes regiões ou indústrias pode causar confusão e dificuldades na implementação de procedimentos de calibração.
- Atualização da Documentação: Algumas vezes, a documentação necessária não é atualizada para refletir novas normas ou requisitos regulatórios.
- Capacitação Limitada: Falta de conhecimento sobre todas as regulamentações pertinentes pode resultar em não conformidade.
Para lidar com este desafio, é fundamental que as empresas mantenham um acompanhamento contínuo das regulamentações em suas respectivas indústrias e ofereçam treinamento adequado às equipes envolvidas na calibração. Além disso, considerar a consultoria de especialistas em conformidade pode ser uma abordagem útil.
Integração de Tecnologias Avançadas
Com o avanço das tecnologias, a integração de novas soluções e ferramentas pode representar desafios significativos na calibração de instrumentos. A transição de sistemas antigos para novos pode causar interrupções temporárias e a curva de aprendizado pode ser acentuada.
Os principais desafios nesse contexto incluem:
- Adoção de Novas Tecnologias: A resistência à adoção de novas tecnologias pode adiar a atualização dos processos requeridos.
- Perda de Dados Durante a Transição: O risco de perda de dados durante a migração para novos sistemas pode ser uma preocupação crítica.
- Necessidade de Treinamento Contínuo: Tecnologias avançadas frequentemente exigem treinamento adicional para garantir que a equipe esteja apta a operar novos instrumentos.
Para superar esses obstáculos, as empresas devem planejar cuidadosamente a implementação de novas tecnologias e assegurar que haja suporte contínuo e treinamento. O envolvimento da equipe no processo de seleção de novas ferramentas também pode aumentar a aceitação e o engajamento.
Além de todos os desafios mencionados, é importante destacar a importância da calibração contínua e eficaz no ambiente industrial. Apesar das dificuldades, a implementação de melhores práticas e uma cultura organizacional que valoriza a calibração pode levar a melhorias significativas na produtividade, qualidade e segurança operacional.
A superação desses desafios exige um compromisso genuíno de todos os níveis da organização. A colaboração de equipes multidisciplinares e uma abordagem proativa são essenciais para garantir que a calibração de instrumentos seja não apenas uma tarefa de conformidade, mas uma estratégia fundamental para a excelência operacional.
Manutenção e Monitoramento de Instrumentos Calibrados
A manutenção e o monitoramento de instrumentos calibrados são práticas essenciais para garantir a precisão, a eficiência e a segurança nas operações industriais. A calibração é um processo crítico que assegura que os instrumentos estejam medindo com exatidão, mas a manutenção e o monitoramento regulares são igualmente importantes para prolongar a vida útil dos equipamentos e evitar falhas. Neste segmento, discutiremos as melhores práticas para a manutenção e o monitoramento de instrumentos calibrados, abordando sua importância, estratégias eficazes e desafios comuns.
Importância da Manutenção Regular
A manutenção regular dos instrumentos é fundamental para garantir que eles operem de maneira consistente e segura. Quando equipamentos não são mantidos adequadamente, eles podem se desgastar, o que resulta em medições imprecisas que podem comprometer a qualidade do produto e a segurança operacional.
Entre os benefícios da manutenção regular, podemos citar:
- Garantia da Precisão: Instrumentos bem mantidos têm menos probabilidade de apresentar desvios e, portanto, são mais confiáveis nas medições.
- Aumento da Vida Útil: Através da manutenção preventiva, é possível identificar e corrigir problemas antes que eles levem a falhas catastróficas.
- Custo-Efetividade: Investir em manutenção pode ser mais econômico do que lidar com as conseqüências de paradas inesperadas e reparos extensivos.
Além disso, a manutenção regular ajuda a cumprir requisitos de conformidade e regulatórios, que exigem que os instrumentos sejam mantidos em condições de trabalho ideais.
Estratégias de Manutenção
Existem diversas estratégias de manutenção que podem ser aplicadas aos instrumentos calibrados, cada uma com suas vantagens e desvantagens. Algumas das mais comuns incluem:
Manutenção Preventiva
A manutenção preventiva envolve a realização de inspeções e serviços em intervalos regulares, independentemente do estado aparente do equipamento. Isso ajuda a garantir que os instrumentos estejam sempre prontos para uso e reduz a probabilidade de falhas inesperadas.
- Programação de Inspeções: Estabelecer uma programação regular para inspeções e serviços que inclui verificação de componentes críticos.
- Substituição de Peças: Trocar partes suscetíveis de desgaste conforme necessário, utilizando cronogramas que se baseiam em dados históricos de desempenho.
- Limpeza: Garantir que os instrumentos sejam mantidos limpos e em condições ideais de funcionamento.
Manutenção Corretiva
A manutenção corretiva refere-se à abordagem reativa que envolve reparar ou substituir componentes quando eles falham. Embora esta estratégia possa parecer mais econômica, ela muitas vezes resulta em custos mais altos devido a paradas inesperadas e reparos extensivos.
- Identificação Rápida de Problemas: Ter um sistema eficaz para identificar e reportar problemas rapidamente é essencial para a manutenção corretiva.
- Redução do Tempo de Inatividade: Implementar processos que minimizem o tempo de inatividade após as falhas é crucial para as operações.
- Avaliação de Causas Raiz: Após a correção, realizar uma análise para entender a causa raiz da falha e evitar que se repita.
Manutenção Preditiva
A manutenção preditiva utiliza tecnologia e análise de dados para prever quando um instrumento pode falhar, permitindo a realização de serviços antes que isso aconteça. Essa abordagem ajuda a reduzir os custos com paradas inesperadas e melhora a eficiência operacional.
- Monitoramento em Tempo Real: Utilizar sensores e sistemas de monitoramento para acompanhar o desempenho dos instrumentos em tempo real.
- Dados Analíticos: Analisar dados históricos para prever falhas e determinar os melhores momentos para realizar manutenção.
- Ajustes Proativos: Realizar ajustes em vez de esperar por falhas para maximizar a eficiência e minimizar o risco.
Monitoramento Contínuo
O monitoramento contínuo é uma prática que complementa a manutenção regular, pois permite a avaliação constante da condição dos instrumentos. Através do uso de tecnologia, como sensores e software, as empresas podem rastrear o desempenho dos instrumentos em tempo real e identificar problemas antes que eles se tornem críticos.
As vantagens do monitoramento contínuo incluem:
- Detecção de Anomalias: A capacidade de identificar rapidamente anomalias ou desvios no desempenho do equipamento.
- Redução do Tempo de Inatividade: O monitoramento contínuo permite manutenções programadas e minimiza as interrupções nas operações.
- Relatórios e Análises: A coleta de dados pode gerar relatórios úteis para análise de desempenho ao longo do tempo.
Logística de Manutenção
Um dos aspectos críticos da manutenção e monitoramento é a logística envolvida na execução dessas práticas. Implementar uma logística eficiente é essencial para garantir que a manutenção ocorra de maneira eficaz e oportuna.
- Gestão de Estoque de Peças: Manter um estoque adequado de peças de reposição é fundamental para evitar atrasos em manutenções necessárias.
- Programação de Serviços: Criar um cronograma de manutenção que não interfira na produção é importante para o bom andamento das operações.
- Equipes de Manutenção Qualificadas: A formação de uma equipe habilitada e experiente é imperativa para realizar manutenções com eficiência e segurança.
Documentação e Registro
A documentação e os registros desempenham um papel vital na manutenção e monitoramento de instrumentos. Esta prática assegura que todas as manutenções e calibrações sejam não apenas realizadas adequadamente, mas também documentadas para referência futura.
- Relatórios de Manutenção: Cada manutenção deve gerar um relatório que documente o serviço realizado, as partes substituídas e quaisquer observações relevantes.
- Histórico de Calibração: Manter um histórico completo de todas as calibrações realizadas é essencial para garantir a conformidade com normas.
- Facilidade de Acesso: As informações devem ser armazenadas de uma forma acessível e fácil de consultar, seja em formato digital ou físico.
Desafios na Manutenção e Monitoramento
Apesar da importância da manutenção e do monitoramento, várias dificuldades podem surgir nesse processo. Identificar esses desafios é crucial para desenvolver soluções eficazes.
Custo da Manutenção
Um dos desafios mais evidentes é o custo. A manutenção regular pode ser dispendiosa, especialmente em setores que dependem de equipamentos complexos e caros. Além disso, pode existir resistência de algumas partes da organização a alocar orçamentos para manutenções que não são percebidas como urgentes.
Tempo e Interrupções
A realização de manutenção pode levar a quedas temporárias na produção. Isso se torna um desafio quando a programação de manutenções não é feita de forma a minimizar o impacto nas operações diárias.
Complexidade das Tecnologias
À medida que a tecnologia avança, a complexidade dos instrumentos aumenta, tornando mais difícil não apenas realizar manutenções, mas também monitorar seu desempenho. Sempre que novas tecnologias são introduzidas, há também a necessidade de treinamento adequado, que pode ser um recurso limitado.
Desmotivação das Equipes
Se as equipes não forem incentivadas ou voltadas para a importância da manutenção e monitoramento, isso pode resultar em desmotivação e até mesmo negligência das práticas vitais.
Falta de Padrões e Procedimentos Consolidados
Uma falta de padrões claros para a manutenção e monitoramento pode levar a inconsistências nas práticas, resultando em medições imprecisas e, consequentemente, em problemas maiores na produção.
Como Superar Desafios
Embora existam desafios significativos, estratégias eficazes podem ser implementadas para superá-los:
- Treinamento Contínuo: Investir na formação contínua das equipes de manutenção é crucial para garantir que os técnicos estejam familiarizados com as últimas tecnologias e práticas.
- Planejamento Proativo: O desenvolvimento de um plano abrangente de manutenção que inclui programações apropriadas e melhores práticas pode ajudar a minimizar interrupções.
- Envolvimento da Gestão: A alta administração deve apoiar as atividades de manutenção, proporcionando recursos materiais e humanos adequados.
- Incentivos e Reconhecimento: Criar um sistema de incentivos que reconheça as equipes que executam a manutenção eficazmente pode aumentar a motivação e o comprometimento.
Conclusão
A manutenção e o monitoramento de instrumentos calibrados são processos críticos que não podem ser negligenciados. Eles garantem a precisão das medições, aumentam a eficiência operacional e mantêm a segurança do ambiente de trabalho. Embora existam desafios, investimentos em estratégias de manutenção eficazes e um foco em melhores práticas podem levar a resultados significativos, contribuindo para o sucesso a longo prazo das operações industriais. Se implementadas com diligência e comprometimento, a manutenção e o monitoramento se transformarão em componentes valiosos do sucesso organizacional.
Em conclusão, a calibração de instrumentos industriais é essencial para assegurar medições precisas e confiáveis, fundamentais para a qualidade e segurança em diversas operações. A compreensão da importância da calibração, dos métodos disponíveis e dos desafios enfrentados permite que as empresas adotem práticas eficazes na manutenção e monitoramento de seus instrumentos. Ao priorizar a calibração, as organizações não apenas garantem a conformidade com normas regulatórias, mas também fortalecem sua reputação de confiabilidade no mercado. Dessa forma, investir em calibração e manutenção adequadas se traduz em benefícios tangíveis, como eficiência operacional, redução de custos e a entrega de produtos de alta qualidade. É essencial que as empresas adotem uma abordagem proativa em relação à calibração, garantindo que seus instrumentos estejam sempre prontos para atender aos desafios do dia a dia e contribuindo assim para o êxito de suas operações industriais.