Calibração de Instrumentos Industriais: Importância e Como Fazer
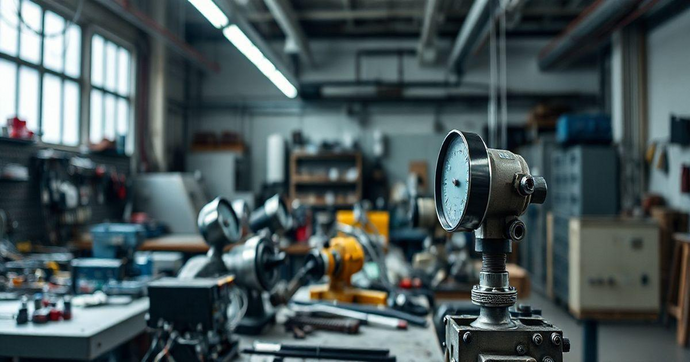
Por: Mauricio - 26 de Dezembro de 2024
Calibração de instrumentos industriais é um processo fundamental para garantir a precisão e a confiabilidade das medições em diversos setores. Com o aumento das exigências de qualidade e eficiência nas indústrias, entender a importância da calibração se torna essencial. Neste artigo, abordaremos como realizar a calibração, os tipos de instrumentos que precisam desse processo, quando e como fazê-lo, além de analisar suas implicações para a qualidade do produto final. Continue lendo para aprofundar seus conhecimentos sobre esse tema vital na indústria.
Importância da Calibração de Instrumentos Industriais
A calibração de instrumentos industriais é um aspecto crucial para garantir que as medições feitas por dispositivos de medição estejam dentro das especificações e tolerâncias exigidas. Em indústrias onde a precisão é vital, a calibração desempenha um papel significativo na manutenção da qualidade, segurança e eficiência operacional. Sem um processo de calibração adequado, as medições podem ser imprecisas, levando a falhas na produção, desperdícios e até mesmo riscos à segurança dos colaboradores.
Um dos principais motivos pelos quais a calibração é tão importante é que ela assegura a conformidade com as normas e regulamentações da indústria. Muitas organizações são obrigadas a cumprir normas específicas que garantem que os produtos atendam a padrões de qualidade e segurança. Por exemplo, indústrias como farmacêutica, alimentícia e eletrônica possuem rigorosos processos de controle de qualidade. A calibração regular dos instrumentos de medição ajuda as empresas a atribuir confiança aos seus processos e a evitar multas ou sanções regulatórias.
Além da conformidade, a calibração efetiva pode impactar diretamente a eficiência da produção. Quando os instrumentos não são calibrados corretamente, existe a probabilidade de que as máquinas operem fora dos parâmetros ideais, resultando em perdas de tempo e material. Por exemplo, um equipamento que mede a pressão ou a temperatura de forma imprecisa pode resultar em processos que não rodam na eficácia máxima. Isso não apenas aumenta custos operacionais, mas também pode diminuir a vida útil dos equipamentos, gerando a necessidade de manutenções mais frequentes.
Outro ponto importante a considerar é a reputação da empresa. Clientes e parceiros de negócios confiam que as empresas que produzem seus produtos estão utilizando métodos e práticas que garantem a qualidade. Se uma empresa falha na calibração de seus instrumentos e isso resulta em produtos defeituosos, a confiança do cliente pode ser abalada. A reputação de uma empresa é um ativo valioso, e a calibração correta dos instrumentos é uma forma de assegurar a qualidade e a confiabilidade que os clientes esperam.
Investir na calibração de instrumentos não é apenas uma questão de conformidade ou eficiência, mas também uma questão de economia. Embora possa parecer um custo inicial elevado, a calibração regular pode resultar em economias significativas a longo prazo, ajudando a evitar desperdícios, retrabalhos e a redução no tempo de produção. Ao optar por uma Empresa de calibração confiável, as indústrias podem garantir que seus instrumentos estão em funcionamento ideal e que as medições realizadas são exatas e consistentes.
Além disso, a calibração de instrumentos contribui para a segurança no ambiente de trabalho. Muitas vezes, instrumentos de medição são usados para monitorar condições críticas, como pressão, temperatura e níveis químicos. Se esses instrumentos falharem ou estiverem desajustados, eles podem causar acidentes graves, colocando em risco a vida dos colaboradores. Portanto, a calibração não apenas garante a precisão nas medições, mas também protege a saúde e a segurança da equipe.
Por fim, a análise de dados gerados por medições é another aspecto que é impactado pela calibração. Empresas que utilizam dados de medições não calibrados podem fazer diagnósticos incorretos ou tomar decisões errôneas sobre processos. Com parâmetros e medições precisas, as empresas podem realizar análises significativas que levam a melhorias contínuas em seus processos de produção.
Em suma, a calibração de instrumentos industriais é fundamental para garantir a precisão, conformidade, eficiência, segurança e reputação no mercado. Ignorar a calibração não é uma opção viável para empresas que buscam não apenas sobreviver, mas prosperar em um ambiente industrial cada vez mais competitivo. Portanto, investir na calibração não é apenas uma prática recomendada; é uma necessidade essencial para a operação eficaz de qualquer indústria.
Tipos de Instrumentos que Precisam de Calibração
A calibração é um processo vital que deve ser realizado em uma variedade de instrumentos industriais para garantir medições precisas e confiáveis. Com o crescimento e a evolução das tecnologias de medição, diversos tipos de instrumentos emergiram, cada um com suas funcionalidades e importância. Neste artigo, discutiremos os principais tipos de instrumentos que precisam ser calibrados e por que essa manutenção regular é essencial.
Um dos instrumentos mais comuns que requer calibração é o medidor de pressão. Este dispositivo é amplamente utilizado em indústrias como a petroquímica, farmacêutica e de alimentos, onde a pressão precisa ser monitorada continuamente. Um medidor de pressão que não está calibrado corretamente pode levar a medições erradas, resultando em prejuízos financeiros e problemas de segurança. Por isso, a manutenção desse tipo de instrumento é crucial, e a escolha de uma Empresa de calibração de equipamentos confiável é fundamental para garantir a precisão dessas leituras.
Outro grupo de instrumentos que requer calibração são os termômetros. Esses dispositivos são essenciais para monitorar e controlar temperaturas em diversos processos industriais, desde a fabricação de alimentos até a produção de medicamentos. Instrumentos de medição de temperatura com falhas podem resultar em produtos fora das especificações aceitáveis ou até na destruição de lotes inteiros. A calibração regular de termômetros é essencial para manter a qualidade e a segurança dos produtos finais.
Os medidores de vazão também são ferramentas críticas que necessitam de calibração. Esses instrumentos são usados para medir a quantidade de líquido ou gás que passa por um ponto específico em um determinado período. Uma medição incorreta de vazão pode afetar a eficiência operacional, aumentando custos e reduzindo a produtividade. Assim como os outros instrumentos mencionados, a calibração de medidores de vazão deve ser realizada de forma sistemática e consistente.
Os instrumentos de medição de nível, como os sensores de nível líquidos e sólidos, também precisam ser calibrados. Esses dispositivos são fundamentais em setores como mineração, controle de resíduos e gestão de água, onde a precisão é crucial para evitar transbordamentos ou operações inseguras. A calibração assegura que as medições de nível estejam dentro de limites seguros e precisos, protegendo tanto os trabalhadores quanto o meio ambiente.
Além dos medidores elencados, a calibração de instrumentos de pesagem não pode ser negligenciada. Balanças utilizadas em indústrias alimentícias, farmacêuticas e químicas devem ser calibradas regularmente para garantir que os produtos sejam pesados corretamente e atendam aos requisitos de conformidade. Uma balança descalibrada pode levar a uma dosagem inadequada de ingredientes, comprometendo não apenas a qualidade do produto, mas também a segurança do consumidor.
Os dispositivos de análise química, como espectrofotômetros e cromatógrafos, também requerem calibração para garantir resultados precisos. Na indústria química e laboratórios de pesquisa, a precisão nas medições pode impactar diretamente o resultado dos experimentos e a qualidade dos produtos finais. A calibração assegura que os dados coletados sejam confiáveis e que as conclusões tiradas a partir deles sejam corretas.
A calibração também é necessária para instrumentos de medição elétricos, como multímetros e osciloscópios. Esses dispositivos são amplamente utilizados na eletrônica e na automação industrial para medir tensão, corrente e resistência. Um multímetro desajustado pode levar a diagnósticos imprecisos, comprometendo a manutenção e a operação de sistemas elétricos. Manter esses instrumentos calibrados ajuda a garantir a confiabilidade de medições e diagnósticos.
Por último, mas não menos importante, os instrumentos de teste e medição de segurança, como detectores de gases e monitores de radiação, exigem calibração rigorosa. Esses dispositivos são essenciais para garantir a segurança dos trabalhadores em ambientes potencialmente perigosos. A calibração regular desses instrumentos é vital para a detecção adequada de perigos e para manter um ambiente de trabalho seguro.
Em resumo, uma ampla gama de instrumentos industriais requer calibração para garantir precisão, segurança e qualidade nos processos de produção. Investir na calibração desses dispositivos não apenas cumpre requisitos de conformidade, mas também protege a reputação da empresa, assegurando produtos de alta qualidade para os clientes. Para garantir a eficácia da calibração, a escolha de uma Empresa de calibração de equipamentos qualificada é essencial para a manutenção e o funcionamento ideal dos instrumentos.
Quando Realizar a Calibração de Instrumentos
Quando se trata da calibração de instrumentos, a questão de quando realizá-la é fundamental para manter a precisão e a confiabilidade nas medições. A calibração não deve ser vista apenas como uma tarefa esporádica, mas como um componente crítico da manutenção de equipamentos e controle de qualidade nas operações industriais. A seguir, abordaremos os principais fatores a serem considerados para determinar a frequência adequada da calibração de instrumentos.
Um dos principais critérios para decidir quando realizar a calibração é o tipo de instrumento utilizado e sua aplicação industrial. Instrumentos que são críticos para o controle de processos, como medidores de pressão, temperatura e vazão, devem ser calibrados mais frequentemente. A natureza dos processos industriais pode levar a um desgaste acelerado dos instrumentos ou a variações nas condições operacionais, o que exige uma calibração regular. Geralmente, recomenda-se que esses dispositivos sejam calibrados pelo menos uma vez ao ano, mas em ambientes críticos, essa frequência pode ser aumentada.
A intensidade de uso também tem um papel crucial na determinação da frequência de calibração. Instrumentos que são utilizados constantemente em operações produtivas estão sujeitos a desgaste e podem se desajustar com mais rapidez. Por outro lado, equipamentos que são usados com menos frequência podem requerer calibração em intervalos mais longos. Uma abordagem inteligente é monitorar o desempenho desses instrumentos e ajustar os programas de calibração de acordo. Se você observa que um instrumento apresenta leituras inconsistentes ou que a precisão diminui ao longo do tempo, isso pode ser um sinal claro de que a calibração precisa ser realizada.
Além disso, eventos que possam impactar a precisão do equipamento devem ser considerados. Por exemplo, se um instrumento sofreu um impacto físico ou foi submetido a condições extremas de temperatura ou pressão, uma recalibração é imprescindível. O transporte e o manuseio inadequado dos instrumentos também podem causar alterações nos ajustes, resultando em medições imprecisas. Portanto, sempre que houver uma situação que possa comprometer a integridade do instrumento, é aconselhável realizar a calibração.
Em muitos setores, a conformidade com normas e regulamentações específicas é uma exigência legal. Muitas vezes, as regulamentações estabelecem intervalos obrigatórios para a calibração de instrumentos para garantir a segurança e a qualidade do produto final. Por exemplo, na indústria farmacêutica, existem requisitos rigorosos para a calibração de equipamentos de medição, e as empresas devem estar em conformidade com essas regras para evitar penalidades. Para assegurar que sua empresa está seguindo todas as diretrizes, ter um programa estruturado de Serviço de calibração é essencial.
Outro fator relevante é a história de desempenho do instrumento. Manter registros de calibração anteriores e diferenças de desempenhos ao longo do tempo pode oferecer insights valiosos sobre a frequência necessária de calibração. Se um instrumento frequentemente apresenta problemas durante as medições, isso pode indicar que o intervalo de calibração precisa ser ajustado ou que o próprio instrumento pode precisar ser substituído.
A manutenção planejada e a análise de tendências de dados também podem orientar a decisão sobre quando realizar a calibração. Ao avaliar os dados coletados ao longo do tempo, sua equipe pode estabelecer padrões que ajudam a prever quando um instrumento pode precisar de calibração. Dessa forma, você pode evitar períodos de inatividade inesperados ou falhas na produção devido a instrumentos desajustados.
Para garantir que você esteja sempre em conformidade com as melhores práticas, a implementação de um cronograma de calibração com base nas necessidades dos instrumentos utilizados é uma tarefa essencial. Isso pode incluir a programação de calibrações periódicas, mas também o ajuste em função da utilização e do desempenho dos equipamentos. Adotar uma abordagem proativa ao longo do tempo ajudará a evitar surpresas indesejadas e garantir de que a qualidade e a precisão sejam mantidas.
Em suma, a calibração de instrumentos deve ser realizada em intervalos regulares, com base em uma série de fatores, incluindo o tipo de instrumento, intensidade de uso, eventos que possam comprometer a precisão, conformidade com regulamentações e desempenho histórico do equipamento. Manter um registro detalhado e implementar um plano de ação bem estruturado são passos fundamentais para assegurar que sua empresa opere de forma eficaz e dentro dos padrões exigidos. Ao priorizar a calibração, você não apenas protege a integridade dos instrumentos, mas também a qualidade dos produtos e serviços oferecidos.
Processo de Calibração: Passo a Passo
A calibração de instrumentos de medição é um processo crítico que assegura a precisão e a confiabilidade das medições realizadas em ambientes industriais. A seguir, apresentaremos um guia passo a passo sobre o processo de calibração, detalhando cada etapa e seus objetivos específicos. Além disso, é importante ressaltar que contar com uma Empresa de calibração de instrumentos de medição pode ser essencial para garantir que esse processo seja realizado de forma adequada e com a precisão necessária.
O primeiro passo na calibração de instrumentos é a verificação inicial. Essa etapa consiste em inspecionar visualmente o instrumento para identificar qualquer dano físico, desgaste ou sinal de que ele possa ter sido desajustado. É crucial garantir que todos os componentes estão em bom estado e funcionando corretamente antes de iniciar o processo de calibração. Essa verificação pode incluir a checagem de cabos, conexões e a leitura inicial do instrumento em condições estáveis.
Uma vez que a verificação inicial é concluída, o próximo passo é a preparação do ambiente de calibração. O ambiente onde a calibração ocorrerá deve ser controlado em termos de temperatura, umidade e outras condições que possam afetar o desempenho do instrumento. Os padrões de calibração devem ser mantidos em condições semelhantes às que o instrumento está sujeito na operação. Um ambiente controlado garante que os resultados da calibração sejam precisos e confiáveis.
Após a preparação do ambiente, é hora de selecionar padrões de referência. Os padrões de calibração são instrumentos de medição que têm uma precisão bem definida e traçada, e que são utilizados como referência. A escolha de padrões de alta qualidade é vital, pois eles vão ser a base para comparar as medições do seu instrumento. Os padrões devem atender a regulamentações específicas e estar disponíveis com certificados de calibração que comprovem sua precisão.
O próximo passo no processo é a realização da calibração propriamente dita. Nesse estágio, o instrumento a ser calibrado é submetido a medições em diferentes pontos de referência. Para isso, o operador utiliza os padrões selecionados e realiza leituras no instrumento a ser calibrado. Os dados coletados são registrados, e as medições são comparadas aos valores de referência. Essa etapa envolve medidas em diversos pontos, assegurando que o instrumento mantenha a precisão em toda a sua faixa de operação.
Com as medições realizadas, o próximo passo é a análise dos resultados. Os dados coletados devem ser examinados cuidadosamente para determinar se as medições do instrumento estão dentro das especificações aceitáveis. Se os resultados indicarem que o instrumento está fora das tolerâncias, ajustes devem ser realizados. Essas correções podem incluir a redefinição de valores, substituição de peças ou outros métodos que assegurem que o instrumento funcione de acordo com as normas apropriadas.
Depois de qualquer ajuste feito, o instrumento deve passar por uma nova série de medições para garantir que as correções foram eficazes. Os resultados das medições pós-ajuste devem ser comparados novamente com os padrões de referência. Se o instrumento estiver dentro das tolerâncias, ele pode ser aprovado e considerado calibrado. Caso contrário, novas correções e medições podem ser necessárias.
Uma vez que o instrumento é considerado calibrado com sucesso, a etapa seguinte é a documentação dos resultados. É fundamental registrar todas as medições realizadas, ajustes feitos e resultados finais em um relatório de calibração. Esse documento deve incluir informações sobre o instrumento, o ambiente de calibração, os padrões utilizados, os dados coletados e qualquer observação relevante. A documentação é essencial não apenas para manter registros precisos, mas também para garantir a conformidade com regulamentos da indústria.
Por último, é importante definir a próxima data de calibração. Com base na frequência de uso do instrumento, condições de operação e normas aplicáveis, um cronograma deve ser estabelecido para garantir que futuras calibragens sejam realizadas de forma consistente. Isso ajuda a manter a precisão das medições e a garantir que mudanças nas condições operacionais não comprometam a confiabilidade do instrumento.
Em resumo, o processo de calibração é essencial para a confiabilidade e precisão de instrumentos de medição. Cada etapa — verificação inicial, preparação do ambiente, seleção de padrões, realização da calibração, análise dos resultados, documentação e definição da próxima calibração — é crucial para garantir que o instrumento atenda aos padrões exigidos. Para empresas que buscam eficiência e precisão, investir em uma Empresa de calibração de instrumentos de medição especializada pode ser a melhor solução para assegurar a qualidade contínua dos processos produtivos.
Métodos de Calibração Utilizados na Indústria
A calibração de instrumentos industriais é essencial para garantir que as medições e dados coletados sejam precisos e confiáveis. Com o avanço das tecnologias de medição, diversos métodos de calibração têm sido desenvolvidos e adotados em diferentes setores da indústria. A escolha do método mais adequado depende de diversos fatores, incluindo o tipo de instrumento, as especificações do fabricante, as condições de operação e os requisitos de precisão. A seguir, exploraremos os principais métodos de calibração utilizados na indústria.
Um dos métodos mais comuns é a calibração por comparação, que envolve a comparação das medições do instrumento a ser calibrado com as medições de um padrão de referência conhecido e rastreável. Esse processo geralmente é realizado em um ambiente controlado, onde o instrumento é exposto a uma série de pontos de referência estabelecidos. A precisão do instrumento é avaliada com base em sua capacidade de reproduzir medições próximas aos valores do padrão de referência. Esse método é amplamente utilizado em indústrias que requerem alta precisão, como a farmacêutica e a alimentícia.
Outro método comum é a calibração por ajuste, que é aplicada quando um instrumento apresenta desvios significativos em relação aos padrões de referência. Nesse caso, procedimentos de ajuste são realizados para corrigir as discrepâncias nas medições. Após realizar os ajustes necessários, o instrumento é submetido novamente à calibração por comparação para garantir que os resultados agora estejam dentro das especificações exigidas. Este método é vital para garantir que equipamentos possam operar dentro de faixas aceitáveis de erro.
Adicionalmente, existe a calibração dinâmica, que é utilizada em instrumentos que medem variáveis em um tempo real, como pressão, temperatura e fluxo. A calibração dinâmica envolve simular as condições reais de operação do equipamento, permitindo que os engenheiros observem como o instrumento responde a diferentes variáveis enquanto simula as condições reais em que o instrumento será utilizado. Essa abordagem fornece uma avaliação prática do desempenho do instrumento e garante que ele se comporte com precisão em condições de operação normais.
Um método que vem ganhando popularidade nos últimos anos é a calibração por software. Com o avanço da tecnologia, muitos instrumentos modernos vêm equipados com sistemas de software que podem realizar autoajustes e gerar relatórios de calibração automaticamente. Esse método simplifica o processo de calibração, assegurando que as medições sejam feitas com precisão. Embora a calibração por software seja eficiente, é crucial que o software utilizado esteja validado e que os procedimentos operacionais padrão sejam seguidos, garantindo que a precisão não seja comprometida.
Outro método relevante é a calibração em campo, que é realizada em situações onde a mobilidade dos instrumentos é um fator crítico. Esse tipo de calibração é frequentemente realizado para dispositivos de medição que não podem ser facilmente removidos de suas instalações permanentes ou que estão em operações contínuas. A calibração em campo pode envolver o uso de equipamentos calibradores portáteis que permitem que os instrumentos sejam verificados e ajustados no local, minimizando o tempo de inatividade e garantindo a continuidade das operações.
A calibração em vários pontos é uma técnica que envolve a verificação da precisão do instrumento em diversas faixas de operação. Normalmente, isso é feito em todos os pontos de operação críticos ou em intervalos definidos. A calibração em vários pontos é especialmente útil para instrumentos que operam em uma ampla gama de medições, pois permite que os engenheiros identifiquem e corrijam problemas de desempenho em diferentes condições operacionais.
Além disso, a calibração respectiva é outro método que é utilizado quando um instrumento de medição tem uma relação linear conhecida com o padrão de calibração. Neste método, a calibração é realizada em um ponto específico, e um intervalo ou gráfico é estabelecido para determinar os pontos de calibração ao longo de todo o alcance de operação do instrumento. Essa técnica é bastante eficaz em aplicações onde a relação entre a variável de interesse e a leitura do instrumento é linear.
Finalmente, a calibração por simulação utiliza modelos matemáticos e algoritmos para reproduzir o comportamento do instrumento a ser calibrado. Este método é frequentemente aplicado em situações onde a calibração direta é difícil ou impossível. A simulação permite prever o desempenho do instrumento em diversas condições, facilitando ajustes baseados em análises cuidadosas, sem a necessidade de intervenções físicas constantes.
Em resumo, a calibração de instrumentos industriais é realizada por meio de vários métodos, cada um com suas vantagens e limitações. Métodos como calibração por comparação, ajuste, dinâmica, software, em campo, em vários pontos, respectiva e simulação oferecem soluções adaptadas às necessidades específicas de diversos setores industriais. Para garantir a precisão e a eficácia das medições, é fundamental que as empresas escolham um método que atenda aos requisitos específicos de seus instrumentos e processos produtivos.
Impactos da Calibração na Qualidade do Produto
A calibração de instrumentos desempenha um papel crucial na manutenção da qualidade dos produtos nas indústrias modernas. À medida que as empresas buscam aumentar sua competitividade e atender às exigências rigorosas do mercado, a calibração se torna uma prática que não pode ser negligenciada. Neste artigo, exploraremos os diferentes impactos da calibração na qualidade do produto, apresentando os benefícios que essa prática traz para os processos produtivos e para a satisfação do cliente.
Um dos principais impactos da calibração na qualidade do produto é a precisão nas medições. Na fabricação de qualquer produto, desde alimentos a componentes eletrônicos, medições precisas são essenciais para garantir que cada item atenda às especificações desejadas. Quando os instrumentos de medição estão corretamente calibrados, eles fornecem resultados confiáveis que ajudam os engenheiros a monitorar e controlar os processos de produção de forma eficaz. Isso, por sua vez, minimiza as chances de erros e não conformidades, resultando em produtos de alta qualidade que atendem ou superam as expectativas dos clientes.
A calibração também desempenha um papel crítico na redução de desperdícios e reprocessamentos. Quando os instrumentos estão desajustados, as medições podem levar a decisões erradas, resultando em perdas significativas de material e tempo. Produtos que não atendem aos padrões devem ser descartados ou retrabalhados, gerando custos adicionais e atrasos na produção. Com a calibração regular, as empresas podem garantir que todos os instrumentos estejam a funcionar dentro de parâmetros aceitáveis, reduzindo assim os níveis de rejeição e promovendo uma utilização mais eficiente dos recursos disponíveis.
Outro impacto significativo é a confiabilidade do produto. Em um mercado onde os clientes são cada vez mais exigentes, a capacidade de garantir a qualidade e a consistência dos produtos é fundamental. A calibração regular assegura que os produtos saiam da linha de produção com qualidade garantida, aumentando a confiança dos clientes e melhorando a reputação da marca. Empresas que investem na calibração de seus instrumentos, portanto, não estão apenas buscando conformidade; estão construindo um relacionamento sólido com seus clientes, baseado na entrega de produtos confiáveis e seguros.
A calibração adequada também afeta a conformidade regulatória. Muitas indústrias, como a alimentícia, farmacêutica e de saúde, são altamente reguladas, e as empresas devem seguir uma série de normas para garantir a segurança e a qualidade dos produtos. A calibração regular dos instrumentos é frequentemente uma exigência legal e, se essas normas não forem atendidas, as empresas podem enfrentar penalidades, multas ou até processos legais. Isso não só tem um impacto financeiro direto, mas também pode prejudicar a reputação da empresa a longo prazo. Portanto, a calibração não é apenas uma questão de melhor eficiência, mas uma estratégia de mitigação de riscos que pode proteger as empresas de consequências legais e financeiras adversas.
Além de tudo isso, a calibração contribui para a inovação contínua dentro das empresas. Ao garantir que os instrumentos estejam funcionando corretamente, as equipes de engenharia e produção podem se concentrar na melhoria dos processos e no desenvolvimento de novos produtos, ao invés de lidar com problemas de qualidade recorrentes. A calibração serve como uma base sólida sobre a qual as inovações podem ser construídas, permitindo que as empresas estejam sempre em posição competitiva no mercado.
Um ponto frequentemente negligenciado é o impacto da calibração na satisfação do cliente. Quando os produtos atendem consistentemente aos padrões de qualidade, os clientes estão mais propensos a ter uma experiência positiva e, por consequência, a se tornarem fiéis à marca. A calibração garante que cada produto esteja em conformidade com as especificações detalhadas, aumentando a probabilidade de satisfação do cliente e, portanto, a lealdade à marca. O feedback positivo dos clientes e as referências boca a boca podem ser um grande motor de crescimento para as empresas que priorizam a calibração como parte de seu compromisso com a qualidade.
Por fim, a calibração de instrumentos é uma prática que tem impacto direto nas métricas de desempenho operacional. Medições precisas e consistentes melhoram a eficácia de processos automatizados, açúcaram a ciclo de produção e permitem um melhor gerenciamento de inventário. Isso resulta em uma operação mais suave e eficiente, contribuindo não apenas para a qualidade dos produtos, mas também para a saúde financeira da empresa. Com menos tempo de inatividade e um uso mais eficiente dos recursos, as empresas podem maximizar seus lucros e manter sua vantagem competitiva.
Em resumo, os impactos da calibração na qualidade do produto são profundos e multifacetados. Desde a precisão nas medições e a redução de desperdícios até a conformidade regulatória e a elevação da satisfação do cliente, os benefícios são inegáveis. A calibração não é apenas uma prática operacional, mas sim uma estratégia que pode definir o sucesso de uma empresa em um mercado competitivo. Portanto, investir em calibração deve ser uma prioridade para qualquer empresa que valoriza a qualidade e a confiabilidade em seus produtos.
Normas e Padrões para Calibração de Instrumentos
A calibração de instrumentos é um fator vital para garantir a precisão e a confiabilidade nas medições realizadas em ambientes industriais. Para que essa calibração ocorra de forma eficaz, é fundamental que os processos estejam alinhados com as normas e padrões estabelecidos, que servem como referência para as melhores práticas da indústria. Neste artigo, examinaremos as principais normas e padrões que regem a calibração de instrumentos, suas aplicações e a importância de seguir essas diretrizes.
Uma das normas mais reconhecidas internacionalmente é a ISO/IEC 17025, que especifica os requisitos gerais para a competência de laboratórios de ensaio e calibração. Essa norma fornece uma estrutura para que os laboratórios demonstrem que operam competentemente e são capazes de produzir resultados válidos. A ISO/IEC 17025 é fundamental para empresas que buscam credibilidade em suas medições, pois abrange tanto os requisitos técnicos quanto a gestão da qualidade. Ter um laboratório acreditado segundo essa norma garante que os processos de calibração atendam a altos padrões de precisão e qualidade.
Outra norma importante é a ISO 9001, que estabelece requisitos para um sistema de gestão da qualidade. Embora não se concentre exclusivamente na calibração, a ISO 9001 exige que as organizações estabeleçam processos que garantam que os produtos e serviços atendam às expectativas do cliente e às regulamentações aplicáveis. A calibração adequada dos instrumentos é parte integrante desse sistema de gestão da qualidade, garantindo que os produtos sejam entregues de acordo com as especificações e requisitos dos clientes.
As normas ASME (American Society of Mechanical Engineers) e API (American Petroleum Institute) também têm padrões relevantes para calibração, especialmente nas indústrias de engenharia mecânica e de petróleo e gás. Esses padrões abordam a calibração de instrumentos para medição de pressão, temperatura, vazão e outros parâmetros críticos, assegurando que os instrumentos operem de forma a proporcionar medições confiáveis. O cumprimento desses padrões é crucial para a segurança e a eficiência nas operações das indústrias afetadas.
No Brasil, as normas da ABNT (Associação Brasileira de Normas Técnicas) também são fundamentais para a calibração de instrumentos. Normas como a NBR ISO/IEC 17025 e a NBR 14000 discutem aspectos relacionados à calibração, qualidade e gestão ambiental. Cumprir essas normas é essencial para que as empresas brasileiras assegurem a qualidade de seus processos, além de facilitar a comercialização em mercados que exigem conformidade com normas internacionais.
Além das normas de gestão e qualidade, existem também padrões metrológicos. O National Institute of Standards and Technology (NIST), nos Estados Unidos, e o Instituto Nacional de Metrologia, Qualidade e Tecnologia (INMETRO), no Brasil, são responsáveis pela pesquisa e desenvolvimento de padrões de medição. Seus padrões fornecem referências para garantir a rastreabilidade das medições, um aspecto crítico na calibração. A rastreabilidade garante que as medições possam ser comparadas a padrões reconhecidos em nível nacional ou internacional, assegurando a precisão e a integridade dos resultados obtidos.
Os padrões de calibração também são específicos para diferentes tipos de instrumentos e medições. Por exemplo, as normas API 20A e API 20B estabelecem diretrizes para a calibração de medições de pressão em equipamentos utilizados na indústria do petróleo. Esses padrões abordam os métodos e as frequências recomendadas de calibração para garantir que as medições estejam dentro dos limites de precisão exigidos pela indústria. Empresas que usam esses padrões demonstram compromisso com a segurança e a eficiência operacional.
A calibração de instrumentos de medição deve ser realizada com base em procedimentos documentados que estejam alinhados às normas e padrões aplicáveis. Estes procedimentos devem incluir especificações detalhadas sobre os métodos a serem utilizados, as condições ambientais sob as quais a calibração deve ser realizada e as frequências recomendadas para a calibração. Ter processos bem documentados ajuda não apenas a garantir a conformidade, mas também a facilitar auditorias e inspeções.
Em resumo, seguir normas e padrões para a calibração de instrumentos é crucial para garantir a precisão e a confiabilidade das medições, essencial para a qualidade dos produtos e serviços oferecidos pelas empresas. Normas como a ISO/IEC 17025, ISO 9001, ASME, API e as diretrizes da ABNT, junto com padrões metrológicos como o NIST e o INMETRO, fornecem as diretrizes necessárias para que as empresas operem de forma eficiente e conforme as expectativas do mercado. A calibração correta contribui não apenas para a conformidade regulatória, mas também para a reputação e o sucesso a longo prazo das organizações no mercado competitivo atual.
Como Escolher um Serviço de Calibração Confiável
A escolha de um serviço de calibração confiável é um fator crítico para garantir a precisão e a confiabilidade das medições em qualquer operação industrial. A calibração adequada dos instrumentos não apenas assegura a qualidade do produto, mas também a segurança dos colaboradores e a conformidade com normas regulatórias. Portanto, selecionar o parceiro ideal para esse serviço é essencial. Neste artigo, abordaremos fatores importantes a serem considerados ao escolher um serviço de calibração confiável.
Um dos primeiros aspectos a se considerar é a acreditação e certificação da empresa de calibração. É fundamental que o fornecedor possua certificações reconhecidas, como a ISO/IEC 17025, que atesta a competência técnica de laboratórios de calibração e teste. Essa acreditação garante que a empresa segue os padrões apropriados, garantindo a qualidade e a integridade dos serviços prestados. Certificações adicionais podem incluir a conformidade com normas de gestão da qualidade, como a ISO 9001, que assegura que o laboratório opera com práticas de gestão bem definidas.
Outro fator importante é a experiência no setor. A experiência da empresa em calibração de instrumentos específicos é um indicativo de que ela conhece os requisitos únicos e as melhores práticas associadas ao seu campo de atuação. Empresas que já atuaram em sua indústria e que têm um bom histórico tendem a entender melhor as nuances de calibração necessária para os equipamentos que você utiliza. Consultar referências ou depoimentos de clientes anteriores pode oferecer insights valiosos sobre a eficácia do serviço.
A gama de instrumentos que o serviço de calibração atende também deve ser analisada. Se a sua empresa usa uma variedade de instrumentos de medição, como termômetros, medidores de pressão e balanças, é crucial que o serviço de calibração seja capaz de atender a todos esses equipamentos. Algumas empresas podem se especializar em tipos específicos de instrumentos, enquanto outras oferecem uma gama completa de serviços. Escolher um serviço que pode lidar com todos os seus equipamentos ajuda a simplificar o processo de calibração e a garantir consistência nos resultados.
Além disso, avaliar a tecnologia e os métodos utilizados pelo serviço de calibração é essencial. A empresa deve utilizar equipamentos modernos e técnicas atualizadas para realizar a calibração. Tecnologias de ponta garantem medições mais precisas e podem oferecer resultados mais rápidos. Pergunte sobre os métodos que a empresa emprega e verifique se eles estão alinhados com as melhores práticas da indústria. A transparência sobre os métodos utilizados é um sinal de que a empresa se preocupa em manter a qualidade.
A disponibilidade e tempo de resposta também são considerações críticas ao escolher um serviço de calibração. Em um ambiente industrial, a ineficiência pode levar a atrasos de produção. Portanto, a empresa de calibração deve ter um histórico comprovado de cumprimento de prazos e deve ser capaz de atender a sua demanda de forma eficiente. Pergunte sobre a possibilidade de lazer calendarizado, assim como a capacidade de realizar calibrações em campo, se necessário, para evitar o tempo de inatividade dos dispositivos.
Outro aspecto a considerar é o suporte ao cliente. A comunicação e a assistência durante todo o processo de calibração são fundamentais. A empresa deve estar disposta a responder suas perguntas, fornecer informações sobre os resultados e explicar os procedimentos utilizados. Um bom serviço de suporte ao cliente não apenas melhora a experiência do usuário, mas também garante que quaisquer problemas ou preocupações que surgirem sejam abordados de forma eficiente. A disposição da empresa em fornecer consultoria e suporte técnico após a calibração é um indicativo de um serviço confiável.
Finalmente, é importante comparar custos e serviços oferecidos. Embora o preço não deva ser o único fator na sua decisão, ele é relevante quando se trata de garantir que o serviço de calibração ofereça um bom valor. Solicite cotações de diferentes fornecedores e verifique o que está incluído no preço. Às vezes, serviços oferecidos a um custo mais baixo não incluem certificação ou relatórios detalhados, que podem ser essenciais para suas operações. Garanta que o custo esteja alinhado com a qualidade e a abrangência do serviço prestado.
Em resumo, a escolha de um serviço de calibração confiável envolve a análise de vários fatores, incluindo acreditação, experiência no setor, gama de instrumentos atendidos, tecnologia utilizada, disponibilidade, suporte ao cliente e custos. Investir tempo na seleção do fornecedor certo não é apenas uma questão de conformidade; é uma estratégia essencial para garantir a precisão, segurança e a eficiência das operações em sua empresa. Utilizar uma empresa de calibração reconhecida, que atenda a todos esses critérios, resultará em um impacto positivo significativo na qualidade do produto e na satisfação do cliente.
Em conclusão, a calibração de instrumentos industriais é uma prática indispensável que não só assegura a precisão das medições, mas também está diretamente relacionada à qualidade do produto final e à eficiência operacional. Ao longo deste artigo, exploramos as etapas cruciais do processo de calibração, os diferentes tipos de instrumentos que requerem calibração, a frequência necessária para esse procedimento e os impactos positivos que a prática traz para as empresas. Ao investir em calibração adequada e em serviços confiáveis, as indústrias podem garantir que seus produtos atendam aos mais altos padrões de qualidade, respeitem as normas regulatórias e elevem a confiança dos clientes. A calibração não é apenas uma medida corretiva, mas sim um invaluable investimento na excelência operacional, na segurança e na reputação das organizações. Portanto, é essencial que todos os envolvidos no setor industrial reconheçam e priorizem a calibração como parte integral de suas operações.