Calibração de Equipamentos de Medição: Guia Completo
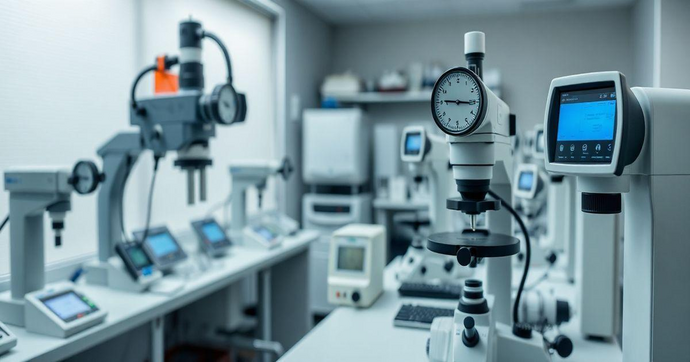
Por: Mauricio - 29 de Dezembro de 2024
A calibração de equipamentos de medição é um processo fundamental que garante a precisão e a confiabilidade dos resultados obtidos. Neste artigo, vamos explorar o que é a calibração, sua importância em diversos setores e os métodos mais eficazes. Ao entender melhor essa prática, você estará mais preparado para garantir a qualidade dos processos e produtos em sua empresa. Continue lendo para descobrir tudo sobre calibração de equipamentos de medição e como implementá-la de forma eficaz.
O que é Calibração de Equipamentos de Medição
A calibração de equipamentos de medição refere-se ao processo de ajustar e verificar a precisão de instrumentos que medem grandezas físicas, como temperatura, pressão, comprimento e voltagem. Este procedimento é essencial para garantir que os equipamentos forneçam resultados confiáveis e consistentes ao longo do tempo. A calibração é um conceito amplamente utilizado em diversas indústrias, incluindo farmacêutica, alimentícia, petroquímica e automotiva, entre outras.
Em termos simples, a calibração envolve comparar as leituras de um equipamento de medição com um padrão conhecido. Esse padrão é, geralmente, um equipamento altamente preciso, que é rastreável a padrões nacionais ou internacionais. Durante o processo de calibração, as divergências entre as leituras do equipamento e o padrão referencial são identificadas e, se necessário, ajustes são feitos para garantir que o instrumento funcione dentro das especificações adequadas.
Existem diferentes métodos de calibração, dependendo do tipo de equipamento e das condições específicas de operação. Por exemplo, a calibração de um termômetro pode envolver o uso de um banho de temperatura controlada, enquanto a calibração de um manômetro pode requerer a aplicação de pressão conhecida usando reguladores de pressão. Independentemente do método utilizado, o objetivo principal da calibração é aumentar a confiabilidade e a precisão das medições.
A importância da calibração de equipamentos de medição não pode ser subestimada. Em muitas indústrias, resultados imprecisos podem levar a consequências graves, como falhas de produtos, problemas de segurança ou prejuízos financeiros. Por exemplo, em um laboratório farmacêutico, a precisão das medições pode afetar a qualidade dos medicamentos produzidos. Portanto, a calibração regular ajuda a evitar erros que podem ter implicações significativas.
Outro ponto crucial a ser considerado é que a calibração não é um evento único; deve ser realizada com regularidade. A frequência ideal para calibração depende de vários fatores, como o tipo de equipamento, a complexidade das medições e o ambiente de operação. Muitos fabricantes e normas, como as da ISO, recomendam a calibração em intervalos específicos, mas as empresas também devem avaliar seu próprio histórico de desempenho e fazer ajustes conforme necessário.
Além disso, a documentação é um aspecto crucial da calibração. Cada calibração realizada deve ser registrada, com detalhes sobre a data, o método utilizado, os resultados e quaisquer ajustes feitos. Isso não apenas proporciona um histórico de manutenção do equipamento, mas também é essencial para auditorias e conformidade com normas de qualidade. Laboratories e empresas que atendem a regulamentações específicas devem ter registros precisos para demonstrar que estão em conformidade com esses requisitos.
Para as empresas que buscam serviços de calibração, é fundamental selecionar uma Empresa de calibração confiável e qualificada. Ao terceirizar a calibração, as empresas podem se beneficiar de uma experiência especializadas, equipamentos avançados e um conhecimento profundo das normas aplicáveis. A escolha de uma empresa que possua acreditações reconhecidas, como ISO 17025, também é um indicador de que ela pode fornecer serviços de calibração de alta qualidade.
Em resumo, a calibração de equipamentos de medição é uma parte vital da garantia da qualidade em diversos setores. O processo ajuda a assegurar que os instrumentos estão fornecendo medições precisas, o que, por sua vez, afeta diretamente a qualidade dos produtos e serviços oferecidos. Com a calibração regular e a escolha de profissionais qualificados, as empresas podem garantir que suas operações não apenas atendam, mas superem as expectativas de qualidade e segurança.
Importância da Calibração em Processos Industriais
A calibração é um aspecto fundamental para qualquer operação industrial que depende de medições precisas. A importância da calibração em processos industriais se revela em várias dimensões que impactam diretamente a eficiência, a segurança e a qualidade dos produtos fabricados. Desde a produção até o controle de qualidade, a calibração assegura que os equipamentos estejam funcionais e proporcionem resultados confiáveis.
Um dos principais objetivos da calibração em indústrias é garantir a precisão das medições. Instrumentos que não estão devidamente calibrados podem levar a medições erradas, resultando em produtos defeituosos, desperdícios e aumento de custos. Com a calibração, as indústrias podem minimiza essas incertezas, garantindo que os parâmetros de produção, como temperatura, pressão e volume, estejam dentro das especificações necessárias para a fabricação de produtos de alta qualidade.
A calibração também desempenha um papel vital na conformidade com as normas e regulamentações do setor. Muitas indústrias são regulamentadas por ê normas que exigem a calibração regular de equipamentos para manter a qualidade e a segurança. Por exemplo, indústrias alimentícias e farmacêuticas precisam atender a rigorosos critérios de controle de qualidade, e a calibração é uma parte essencial desse processo. Empresas com práticas de calibração ineficazes podem enfrentar sérias penalidades, apreensões de produtos e danos a sua reputação no mercado.
Além disso, a segurança é um fator crítico em processos industriais. Equipamentos de medição não calibrados podem causar falhas catastróficas que ameaçam a segurança dos trabalhadores e o ambiente em geral. Por exemplo, em indústrias químicas, a medição imprecisa de gases perigosos pode resultar em vazamentos fatais. A calibração regular de equipamentos de medição, portanto, não apenas melhora a segurança no local de trabalho, mas também protege a empresa de potenciais ações legais e crises de reputação.
A eficiência operacional é outra área na qual a calibração exerce um impacto significativo. Equipamentos calibrados asseguram que as máquinas funcionem de maneira otimizada, evitando interrupções e minimizando o tempo de inatividade. Quando as máquinas estão operando com precisão, o tempo produtivo aumenta, reduzindo custos associados a retrabalhos e reparos. A calibração regular ajuda a prolongar a vida útil do equipamento, impactando positivamente a rentabilidade da empresa.
Um aspecto subestimado, mas igualmente importante, é a confiança que a calibração proporciona. Quando uma empresa pode garantir a qualidade de seus produtos através de medições precisas, ela conquista a confiança de seus clientes. Esta confiança é vital para a fidelização do cliente e pode se traduzir em uma vantagem competitiva significativa no mercado. Indústrias que têm a reputação de oferecer produtos de alta qualidade são souvente preferidas em relação aos concorrentes.
Para empresas que buscam implementar ou melhorar seus processos de calibração, é recomendável consultar uma Empresa de calibração de equipamentos confiável. Profissionais especializados podem não apenas realizar a calibração de forma eficaz, mas também fornecer insights sobre melhores práticas, frequência de calibração e documentação necessária para garantir a conformidade. Esse suporte é crucial para empresas que desejam otimizar seus processos e manter padrões de qualidade elevados.
Outro ponto a ser destacado é a integração da calibração dentro do sistema de gestão da qualidade (SGQ) das indústrias. A calibração deve ser vista como parte integrante do SGQ, sendo necessária para ajudar a atingir os objetivos de desempenho. A implementação de um plano de calibração eficaz torna-se uma atividade estratégica, que pode direcionar investimentos e esforços em melhorias contínuas.
Em resumo, a calibração em processos industriais é de suma importância e impacta diretamente a qualidade, a segurança e a eficiência operacional. A prática regular não só atende às exigências normativas, mas também melhora a confiabilidade dos produtos e serviços oferecidos pela indústria. Portanto, investir em calibração é garantir um padrão elevado de qualidade e segurança, refletindo diretamente na satisfação do cliente e na competitividade no mercado.
Tipos de Equipamentos de Medição Comuns
No mundo da indústria e da ciência, uma ampla variedade de equipamentos de medição é utilizada para garantir que os processos estejam sob controle e funcionem de acordo com parâmetros estabelecidos. Conhecer os tipos de equipamentos de medição comuns é fundamental para entender como a calibração se aplica a cada um deles. A calibração correta garante precisão em medições e resulta em produtos de qualidade superior. Vamos explorar alguns dos principais equipamentos utilizados em diferentes setores.
Um dos equipamentos de medição mais comuns é o termômetro, que é utilizado para medir a temperatura. Existem diversos tipos de termômetros, como os digitais, os de mercúrio e os infravermelhos. Cada um deles possui suas características específicas e aplicações ideais. Por exemplo, termômetros infravermelhos são amplamente usados em ambientes industriais para medir temperaturas de superfícies sem contato direto, enquanto termômetros de mercúrio são frequentemente utilizados em laboratórios para medições precisas em ciclos de teste.
Outro equipamento essencial é o manômetro, que mede a pressão de líquidos e gases. Os manômetros são fundamentais em indústrias químicas e petroquímicas, onde a medição precisa da pressão pode afetar a segurança e a eficiência do processo. Manômetros analógicos e digitais são os mais comuns, cada um com suas vantagens. A calibração regular é necessária para garantir que as leituras de pressão estejam dentro das especificações exigidas.
Os multímetros são outro tipo de equipamento amplamente utilizado, especialmente em ambientes elétricos. Eles medem tensão, corrente e resistência elétrica, tornando-se ferramentas versáteis para eletricistas e engenheiros. A calibração de multímetros é crucial, pois medições imprecisas podem resultar em falhas no sistema elétrico e potenciais riscos à segurança. Além disso, a qualidade do equipamento pode ser avaliada através de medições realizadas com um multímetro devidamente calibrado.
Os higrômetros são equipamentos que medem a umidade do ar e são essenciais em indústrias onde a umidade pode impactar a qualidade do produto, como na indústria alimentícia e farmacêutica. Um higrômetro ineficaz pode resultar em produtos comprometidos devido à umidade inadequada. A manutenção e calibração adequadas são cruciais para garantir que os higrômetros forneçam resultados precisos e confiáveis.
Quando se trata de medição de fluxo, os fluxômetros desempenham um papel significativo. Eles são utilizados para medir a quantidade de líquido ou gás que passa por um ponto em um determinado período de tempo. A calibração de fluxômetros é essencial para a precisão das medições em diversas aplicações, desde saneamento básico até processos industriais complexos. Um fluxo mal medido pode levar a desperdício e problemas de eficiência.
Além desses, os calibres são instrumentos de precisão utilizados para medir dimensões e formas. Eles são amplamente utilizados em indústrias de manufatura e montagem. Tipos comuns de calibres incluem os calipers digitais e analógicos, que ajudam a garantir que as peças sejam produzidas de acordo com as especificações corretas. A calibração de calibres é necessária para evitar desvios na produção que podem resultar em peças inseguros ou ineficazes.
Em adição, os espectrômetros são equipamentos que analisam a composição de materiais através da luz. Eles são usados em uma variedade de campos, desde laboratório de pesquisa até controle de qualidade industrial. A calibração de espectrômetros é vital para garantir que as análises químicas sejam precisas e confiáveis. A confiança nos resultados obtidos pode fazer uma diferença significativa na pesquisa e desenvolvimento de produtos novos.
Com a diversidade de equipamentos de medição disponíveis, é crucial lembrar que cada um desempenha um papel vital nas operações industriais e científicas. A calibração regular é essencial não apenas para manter a precisão, mas também para garantir que as medições estejam sempre dentro dos padrões exigidos. Para as empresas que estão em busca de um Serviço de calibração confiável, é importante escolher fornecedores com a experiência e a certificação necessária. Profissionais qualificados garantem que os equipamentos de medição estejam sempre prontos para fornecer resultados precisos e seguros.
Em resumo, compreender os tipos de equipamentos de medição comuns e a importância de sua calibração nos permite valorizar a precisão dos resultados em processos industriais. Cada equipamento, desde termômetros até espectrômetros, exige atenção e manutenção para garantir que suas medições sejam confiáveis e do mais alto padrão de qualidade. A calibração é um investimento que assegura a durabilidade e eficácia dos equipamentos, facilitando assim operações mais seguras e eficientes em diversas indústrias.
Métodos de Calibração Eficazes
A calibração de equipamentos de medição é um processo vital para garantir a precisão e a confiabilidade dos resultados obtidos em diversos setores. Há vários métodos de calibração eficazes que podem ser aplicados dependendo do tipo de instrumento, da precisão necessária e das condições de operação. Neste artigo, discutiremos alguns dos métodos mais comuns e suas aplicações, proporcionando uma visão abrangente sobre como garantir medições confiáveis.
Um dos métodos mais utilizados é o método da comparação direta. Esse método envolve a comparação das medições do equipamento a ser calibrado com as de um padrão conhecido e rastreável. O equipamento padrão deve ser um instrumento de calibração previamente calibrado e que tenha a precisão requerida. Ao medir a mesma condição com ambos os instrumentos, é possível analisar a diferença entre as leituras, identificar desvios e fazer os ajustes necessários. Esse método é amplamente utilizado em laboratórios e indústrias onde a precisão é crítica.
Outro método eficaz é o método de referência de ponto fixo, que é utilizado principalmente em termômetros e manômetros. Nesse método, estabelece-se uma condição de referência que será utilizada durante a calibração. Por exemplo, no caso de um termômetro, pode-se usar o ponto de fusão do gelo ou o ponto de ebulição da água como referência. As medições são feitas em relação a esses pontos fixos, garantindo que o instrumento esteja calibrado para condições extremas e conhecidas. Isso é especialmente útil para dispositivos que precisam operar em uma ampla faixa de temperaturas.
O método de calibração por ajuste é outro procedimento comumente usado. Após realizar medições de um determinado parâmetro e a comparação com um padrão, este método permite ajustar o instrumento de medição para que ele se alinhe ao padrão. Isso pode envolver a alteração de configurações internas do equipamento ou a substituição de componentes defeituosos. É um método prático que ajuda a restaurar a precisão do instrumento, garantindo que ele continue a funcionar de forma eficaz.
A calibração em circuito fechado é um método que envolve o controle total do ambiente onde a calibração ocorre. Isso significa que todas as variáveis que podem afetar a medição são rigorosamente monitoradas e controladas. Este método é frequentemente utilizado em laboratórios de alta precisão, onde pequenas variações podem ter grande impacto nos resultados. Ao controlar variáveis como temperatura, umidade e pressão atmosférica, os técnicos podem assegurar que a calibração resulte em medições ainda mais precisas.
Um outro método valioso é a calibração sob carga, que é especialmente importante em instrumentos que devem medir sob condições normais de operação. Este método é utilizado, por exemplo, em sistemas de medição de fluxo e peso. Durante a calibração, o equipamento é submetido a condições reais de carga e as medições são comparadas. Isso assegura que os instrumentos forneçam resultados precisos em situações normais de operação, o que é essencial tanto para a segurança quanto para a eficácia operacional.
Utilizar um software de calibração também pode ser extremamente benéfico. Existem diversos softwares disponíveis que permitem acompanhar histórico, agendar calibrações e até mesmo reportar discrepâncias. Esse tipo de sistema ajuda as empresas a manterem suas operações dentro dos padrões normativos e proporciona um controle rigoroso sobre todos os equipamentos. Ao integrar tecnologias na manutenção e calibração, as indústrias podem aumentar a eficiência e a confiabilidade dos dados coletados.
Para empresas que não possuem capacidade interna para realizar calibrações, contratar uma Empresa de calibração de instrumentos de medição especializada é uma decisão inteligente. Essas empresas não só realizam calibrações utilizando métodos eficazes, mas também estão atualizadas sobre as melhores práticas e requisitos normativos. Além disso, elas podem oferecer insights sobre como otimizar processos de calibração e manter a integridade dos dados ao longo do tempo.
Um último método que merece destaque é o método de verificação. Essa técnica envolve a comparação das medições do equipamento com aquelas de um padrão, não necessariamente para realizar um ajuste mas para simplesmente verificar a precisão do instrumento. É um método importante para a manutenção da qualidade em ambientes onde a calibração regular é exigida. A verificação periódica pode ser uma maneira eficaz de garantir que os instrumentos permaneçam dentro das especificações, sem a necessidade de ajustes frequentes.
Em conclusão, a escolha do método de calibração adequado é crucial para manter a precisão e a confiabilidade dos equipamentos de medição. É importante levar em consideração a natureza do equipamento, as exigências do setor e a complexidade do processo. Esses métodos não apenas ajudam a garantir medições precisas, mas também facilitam operações seguras e eficientes nas indústrias. A calibração regular, apoiada por práticas adequadas e, se necessário, a assistência de uma empresa especializada, assegurará que os instrumentos estejam sempre prontos para fornecer dados confiáveis.
Frequência Ideal para Calibração
A frequência ideal para calibração de equipamentos de medição é um dos aspectos mais críticos na manutenção da precisão e confiabilidade das medições. Determinar a frequência correta não é uma tarefa simples, pois depende de diversos fatores que variam de um setor para outro. Neste artigo, vamos explorar as considerações que devem ser levadas em conta para estabelecer a frequência de calibração mais adequada, garantindo assim a manutenção da integridade dos resultados obtidos.
Um dos fatores mais importantes a se considerar na determinação da frequência de calibração é a natureza do equipamento. Equipamentos que operam em condições extremas, como altas temperaturas, pressões elevadas ou em ambientes corrosivos, tendem a necessitar de calibrações mais frequentes. Isso ocorre porque esses fatores externos podem causar desgastes e variações nas medições, levando a resultados imprecisos. Por exemplo, um manômetro utilizado em uma estação de gás deve ser calibrado com mais frequência do que um utilizado em um laboratório de controle de qualidade que opera em condições estáveis.
Outro fator é o uso e desgaste do equipamento. Equipamentos que são utilizados constantemente ou que estão sujeitos a impactos físicos, como balanças industriais ou instrumentos de medição de alta precisão, podem apresentar desvios mais rapidamente do que aqueles que são usados esporadicamente. Portanto, no cronograma de calibração, é fundamental considerar a intensidade e a frequência de uso do equipamento para garantir a confiança nas medições realizadas.
As diretrizes e normas da indústria também desempenham um papel significativo na determinação da frequência de calibração. Muitas indústrias são regidas por regulamentações rigorosas que estabelecem as frequências mínimas de calibração. Setores como farmacêutico, alimentício e petroquímico, por exemplo, têm requisitos específicos relativos à calibração para garantir a segurança e a qualidade dos produtos. É importante estar sempre atualizado sobre as normas regulamentadoras aplicáveis ao seu setor, pois isso pode orientar a definição do plano de calibração.
A história de desempenho do equipamento também deve ser considerada. Se um equipamento apresentou problemas frequentes no passado ou se já foi descalibrado com regularidade, isso pode indicar a necessidade de aumentar a frequência de calibração. Por outro lado, se a ferramenta demonstrou sempre estabilidade e precisão ao longo do tempo, pode ser possível espaçar os intervalos de calibração. Isso pode otimizar os custos operacionais e minimizar o tempo de inatividade do equipamento.
A tecnologia do equipamento também é um fator a ser observado. Equipamentos mais modernos frequentemente possuem tecnologias de monitoramento de desempenho, que podem fornecer dados em tempo real sobre a precisão e a condição do instrumento. Assim, esses dispositivos podem sinalizar quando uma calibração é necessária, permitindo um gerenciamento mais eficiente e baseado em dados, em vez de apenas seguir um cronograma rígido.
Além disso, a manutenção preventiva deve ser incluída na estratégia de calibração. Manutenções regulares e verificações periódicas podem auxiliar na identificação de problemas antes que eles se agravem, permitindo um planejamento mais eficaz das calibrações. Isso se traduz em um ciclo de vida útil mais longo para os equipamentos, além de garantir que eles operem sempre dentro das especificações desejadas.
Para as empresas que buscam um serviço de calibração confiável, contar com a assessoria de fornecedores especializados pode otimizar a frequência de calibração. As empresas de calibração geralmente possuem expertise e conhecimento sobre as melhores práticas do setor, e podem orientar a criação de um plano de calibração adaptado às necessidades específicas de cada cliente. Além disso, isso pode ajudar a garantir que a empresa esteja em conformidade com as regulamentações de segurança e qualidade.
Em resumo, não há um tempo fixo para a calibração dos equipamentos; a frequência ideal deve considerar a natureza do equipamento, o uso, as normas da indústria, e a experiência passada do equipamento. Um plano de calibração bem elaborado não apenas assegura medições precisas e confiáveis, mas também contribui para a segurança operacional e a qualidade dos produtos finais. A calibração regular e cuidadosa é um investimento que, a longo prazo, se refletirá em eficiência e confiabilidade operacional, além de garantir a satisfação do cliente.
Finalmente, a implementação de um cronograma que se ajusta às variáveis mencionadas ajuda a promover um ambiente de trabalho mais seguro e eficiente, ao mesmo tempo que minimiza custos e otimiza o uso do equipamento. Em indústrias onde a precisão é crítica, a calibração deve ser uma prioridade, assegurando que as ferramentas e equipamentos estejam sempre prontos para fornecer resultados de alta qualidade.
Erros Comuns na Calibração de Equipamentos
A calibração de equipamentos de medição é uma prática essencial para garantir a precisão e a confiabilidade das medições. Contudo, existem erros comuns na calibração de equipamentos que podem comprometer a qualidade do processo e afetar os resultados finais. Neste artigo, abordaremos alguns desses erros e como evitá-los, ajudando a garantir que as medições permaneçam precisas e confiáveis.
Um dos erros mais frequentes acontece na seleção inadequada do equipamento de referência. A calibração envolve a comparação entre o equipamento a ser calibrado e um padrão conhecido. Se o equipamento de referência não for calibrado adequadamente, ou se não atender aos requisitos necessários, os resultados da calibração do equipamento alvo estarão comprometidos. Portanto, é fundamental garantir que o equipamento de referência seja rastreável e possua as características apropriadas para as medições desejadas.
Outro erro comum é a omissão de condições ambientais. A calibração deve ser realizada em um ambiente controlado para que condições como temperatura, umidade e pressão não influenciem os resultados. Por exemplo, calibrações realizadas em um ambiente com grandes variações de temperatura podem levar a resultados imprecisos. Portanto, é essencial que as condições ambientais sejam monitoradas e mantidas dentro dos limites especificados durante o processo de calibração.
A falta de treinamento adequado dos técnicos responsáveis pela calibração também é um erro significativo. Profissionais não treinados podem não entender completamente os métodos de calibração ou as especificações do equipamento que estão calibrando. Isso pode levar a medições incorretas e ajustes inadequados. Investir na formação contínua dos profissionais é crucial para assegurar que eles estejam atualizados com as melhores práticas e procedimentos de calibração.
Um erro bastante comum refere-se à documentação inadequada. A manutenção de registros precisos e detalhados é essencial para auditorias e conformidade. Muitas vezes, os técnicos podem negligenciar a documentação, ou registrá-la de maneira incorreta, o que pode resultar em lacunas sobre a história de calibração de um equipamento. Essa falta de registros pode dificultar a manutenção de protocolos de qualidade e pode levar a erros no futuro. Portanto, também é importante implementar um sistema rigoroso de documentação e rastreamento de calibrações realizadas.
Além disso, um erro na execução inadequada dos procedimentos de calibração pode ocorrer quando os protocolos estabelecidos não são seguidos corretamente. Cada equipamento possui um procedimento específico que deve ser seguido para garantir a precisão das medições. Ignorar etapas ou fazer alterações não autorizadas durante o processo de calibração pode resultar em desvios nas medições. O uso de listas de verificação pode ajudar a garantir que todos os passos sejam realizados corretamente.
A calibração em intervalos inadequados também é uma preocupação importante. Não realizar calibrações com a frequência recomendada pode levar a medições imprecisas. Por outro lado, calibrações excessivas podem resultar em desgaste desnecessário do equipamento. Estabelecer um cronograma equilibrado para calibrações e realizar verificações regulares pode ajudar a evitar esse tipo de erro.
Um erro comum que muitos técnicos cometem é a insuficiência na verificação pós-calibração. Após a calibração, é vital realizar verificações para assegurar que o equipamento esteja realmente funcionando dentro das especificações estabelecidas. Ignorar essa etapa pode significar que um erro não foi corrigido e que o equipamento não está confiável. Realizar testes depois da calibração é uma prática recomendada para garantir a eficácia do processo.
Além disso, é importante estar ciente do uso de equipamentos de calibração inadequados. Cada tipo de equipamento de medição possui requisitos específicos que devem ser atendidos durante a calibração. Utilizar ferramentas de calibração que não são compatíveis ou que não estão em boas condições pode levar a erros. É primordial utilizar equipamentos adequados e bem mantidos para assegurar a precisão das medições.
Por fim, outro erro que pode ocorrer é a não consideração das especificações do fabricante. Cada equipamento tem seus próprios padrões e requisitos de calibração que devem ser seguidos. Ignorar as especificações e recomendações do fabricante pode resultar em calibrações que não atendem às necessidades do equipamento, o que compromete a precisão das medições. Assim, sempre que realizar a calibração, é vital estar ciente das orientações do fabricante e segui-las rigorosamente.
Em resumo, a calibração de equipamentos de medição é uma tarefa que requer atenção e precisão para evitar erros comuns que podem comprometer o processo. A seleção adequada de equipamentos, controle das condições ambientais, treinamento contínuo dos profissionais, documentação rigorosa, execução correta dos procedimentos, intervalo de calibração apropriado, verificação pós-calibração, uso de ferramentas adequadas e consideração das especificações do fabricante são fatores essenciais. Ao implementar práticas eficazes e evitar esses erros comuns, você pode garantir medições precisas e confiáveis que são fundamentais para a qualidade e segurança nos processos industriais.
Normas e Padrões de Calibração
As normas e padrões de calibração são elementos cruciais que asseguram a qualidade e a confiabilidade das medições em diversos setores industriais e científicos. A adoção dessas normas não só ajuda a garantir a precisão das medições, mas também promove a segurança e a conformidade com as regulamentações vigentes. Neste artigo, discutiremos as principais normas de calibração, sua importância e como implementá-las em processos industriais e laboratoriais.
Uma das normas mais reconhecidas no mundo da calibração é a ISO/IEC 17025. Esta norma estabelece os requisitos gerais para a competência de laboratórios de ensaio e calibração. A conformidade com a ISO/IEC 17025 é essencial para laboratórios que desejam demonstrar sua capacidade técnica e garantir que suas medições e relatórios possam ser aceitos em todo o mundo. Essa norma abrange não apenas os requisitos técnicos, mas também os requisitos de gestão da qualidade que um laboratório deve seguir para assegurar a precisão e a confiabilidade dos resultados.
Outra norma relevante é a ANSI/NCSL Z540, que é uma norma nacional dos Estados Unidos que fornece diretrizes sobre a calibração de equipamentos de medição. Essa norma assegura que o equipamento calibrado possa ser rastreado a padrões nacionais, aumentando a confiança nas medições. A ANSI/NCSL Z540 é particularmente importante em setores onde o controle rigoroso da qualidade é necessário, como nas indústrias de semicondutores e farmacêutica.
A ISO 9001 também possui um papel significativo nas práticas de calibração. Embora seja uma norma de sistema de gestão da qualidade, ela inclui requisitos que se aplicam a processos de calibração. A ISO 9001 exige que as organizações garantam que seus equipamentos estejam calibrados e que as medições sejam mantidas dentro dos limites especificados. Integrar práticas de calibração dentro do sistema de gestão de qualidade ajuda as organizações a melhorarem seu desempenho e a oferecerem produtos e serviços de alta qualidade.
Adicionalmente, normas como a ISO 10012 fornecem diretrizes específicas para a gestão da medição. Essa norma oferece um framework para garantir a precisão e a rastreabilidade das medições, sendo indicada para organizações que precisam de um controle rigoroso sobre suas medições e processos. A ISO 10012 destaca a importância de se documentar todo o processo de calibração e a rastreabilidade das medições ao longo do tempo, o que contribui para a qualidade dos produtos e a confiança do cliente.
A IEC 61508 é outra norma que aborda a segurança funcional de sistemas elétricos, eletrônicos e programáveis, que, em muitos casos, envolvem processos de calibração. Esta norma é aplicada em indústrias onde a segurança é crítica e estabelece requisitos de desempenho para eliminar ou reduzir o risco de falhas. O cumprimento da IEC 61508 é vital em setores como energia, automação e transporte, onde a calibração precisa pode impactar a segurança pública e operacional.
Implementar as normas e padrões de calibração requer um processo estruturado. Inicialmente, a gestão deve identificar quais normas são aplicáveis ao seu setor e às suas operações. A próxima etapa envolve a formação de uma equipe responsável pela implementação e monitoração do cumprimento das normas selecionadas. Essa equipe deve avaliar quais práticas atuais precisam ser ajustadas para alinhar a organização com os requisitos das normas escolhidas.
A empresa de calibração correta pode ajudar nesse processo, oferecendo orientação especializada e serviços de calibração conforme as especificações das normas aplicáveis. Ter acesso a especialistas que compreendem as nuances de cada norma e como aplicá-las de maneira eficaz pode facilitar a transição e garantir que a organização esteja em conformidade com todos os requisitos necessários.
Além disso, a documentação é um aspecto crucial do processo. Manter registros precisos, que incluam detalhes sobre as calibrações realizadas, equipamentos utilizados, padrões de referência e resultados obtidos, é fundamental para assegurar a rastreabilidade e a conformidade. Esses documentos devem ser facilmente acessíveis para auditorias e revisões, ajudando a demonstrar a conformidade com as normas e a eficácia dos processos de calibração implementados.
Por fim, o treinamento contínuo da equipe é vital. À medida que novas normas são introduzidas e atualizações são feitas nas já existentes, a equipe precisa ser informada e treinada sobre as melhores práticas e requisitos dessas normas. Adotar uma cultura de melhoria contínua em torno da calibração e da qualidade permitirá que a organização não apenas atenda, mas supere os requisitos normativos e expectativas dos clientes.
Em suma, as normas e padrões de calibração são essenciais para qualquer organização que busca garantir a precisão e a confiança nas medições. A implementação bem-sucedida dessas normas não apenas assegura a conformidade regulatória, mas também melhora a qualidade dos produtos e serviços oferecidos. Ao considerar a calibração como parte integrante do processo de gestão da qualidade, as empresas podem construir uma base sólida para operações bem-sucedidas e sustentáveis a longo prazo.
Benefícios da Calibração Regular para Empresas
A calibração regular de equipamentos de medição é uma prática essencial que traz diversos benefícios para as empresas. Seja em indústrias, laboratórios ou empresas de serviços, a calibração consistente é fundamental para garantir a qualidade, a segurança e a eficiência dos processos. Neste artigo, discutiremos os principais benefícios da calibração regular e como ela pode impactar positivamente os negócios.
Um dos benefícios mais evidentes da calibração regular é a precisão nas medições. Equipamentos de medição que não são calibrados corretamente podem gerar resultados imprecisos, levando a decisões equivocadas e produtos defeituosos. Isso é especialmente crítico em setores como farmacêutico, alimentício e elétrico, onde a precisão é fundamental. Com a calibração regular, as empresas podem minimizar o risco de erros, garantir que seus produtos atendam aos padrões de qualidade desejados e, consequentemente, aumentar a satisfação do cliente.
Outro ponto importante a se destacar é a conformidade com normas e regulamentos. Muitas indústrias são regulamentadas por normas que exigem a calibração regular de equipamentos para garantir que estejam operando dentro das especificações necessárias. Não cumprir essas regulamentações pode resultar em penalidades, multas, ou até mesmo a interrupção das operações. Ao realizar calibrações regulares, as empresas não apenas evitam problemas legais, como também demonstram um compromisso com a qualidade e a responsabilidade social.
Além disso, a calibração regular contribui para a aumento da eficiência operacional. Quando os equipamentos estão devidamente calibrados, eles funcionam de forma mais eficaz e consistente. Isso se traduz em menos tempo de inatividade, menos retrabalho e menos desperdício de materiais. Ao otimizar os processos de produção e operação, as empresas podem aumentar sua produtividade e reduzir custos, o que resulta em uma melhor margem de lucro. Arrematar eficiência é diretamente proporcional a melhora competitiva no mercado.
A rede de confiança com os clientes também é fortalecida através da calibração regular. Quando uma empresa pode garantir a qualidade dos produtos e serviços que oferece, ela conquista a confiança e a lealdade do cliente. Isso é particularmente importante em mercados saturados, onde a concorrência é intensa. A reputação de oferecer produtos de alta qualidade pode se tornar um diferencial competitivo e levar a um aumento nas vendas e na retenção de clientes.
Ademais, a calibração regular auxilia no alongamento da vida útil dos equipamentos. Equipamentos que são mantidos em condições ideais através de calibrações regulares tendem a ter uma vida útil mais longa. A degradação causada pelo uso constante pode ser minimizada através da manutenção constante, resultando em menos necessidade de investimentos em substituições e reparos. Isso ajuda as empresas a economizar em custos de capital e a maximizar o retorno sobre seus investimentos em equipamentos.
Outro benefício que não pode ser ignorado é a redução de riscos de segurança. Equipamentos que não estão devidamente calibrados podem levar a falhas catastróficas, comprometendo a segurança dos funcionários e a integridade das instalações. Em ambientes onde materiais perigosos são utilizados, a precisão das medições é vital para evitar acidentes. A calibração regular ajuda a garantir que todos os equipamentos estejam funcionando corretamente, contribuindo para um ambiente de trabalho mais seguro.
A calibração também facilita a implementação de melhorias contínuas nas operações. Com a coleta e análise de dados de medições precisas, as empresas podem identificar áreas que requerem melhorias e implementar soluções para otimizar processos. Por exemplo, se forem constatadas medições inconsistentes em uma linha de produção, isso pode ser um sinal de que uma máquina precisa ser ajustada ou que o processo deve ser modificado. A calibração regular fornece a base necessária para decisões informadas que levam a melhorias contínuas.
Além disso, a calibração regular promove um ambiente de responsabilidade e qualidade dentro da organização. Quando as equipes são treinadas para valorizar a calibração e a manutenção dos equipamentos, cria-se uma cultura organizacional que prioriza a qualidade e a precisão. Isso pode impactar positivamente a moral e a motivação dos funcionários, sabendo que estão contribuindo para a entrega de produtos e serviços de alta qualidade.
Finalmente, contar com um serviço de calibração confiável fornece suporte profissional que ajuda a garantir que todos os aspectos da calibração sejam tratados de forma adequada. Empresas especializadas oferecem conhecimento técnico, equipamentos de ponta e um entendimento aprofundado das normas e regulamentações aplicáveis. Isso não apenas facilita as operações de calibração, mas também assegura que a empresa esteja em conformidade com as melhores práticas da indústria.
Em conclusão, os benefícios da calibração regular para empresas são vastos e impactam vários aspectos da operação. Desde a precisão nas medições e conformidade com normas até a eficiência operacional e redução de riscos, a calibração regular é uma prática que deve ser integrada na cultura organizacional. Ao priorizar a calibração, as empresas não apenas melhoram a qualidade de seus produtos e serviços, mas também otimizam seu desempenho geral no mercado. Portanto, a calibração não deve ser vista como um mero requisito, mas sim como uma estratégia essencial para o sucesso a longo prazo de qualquer organização.
Em suma, a calibração de equipamentos de medição é um componente essencial para manter a precisão, a qualidade e a confiabilidade nos processos produtivos de qualquer setor. Ao reconhecer a importância da calibração, as empresas não apenas garantem a conformidade com as normas e regulamentos, mas também promovem a segurança e o bem-estar em suas operações. Com a adoção dos métodos adequados e a realização de calibrações regulares, é possível evitar erros dispendiosos, minimizar riscos e maximizar a eficiência operacional. Portanto, investir em calibração é investir na qualidade dos produtos e serviços oferecidos, resultando em um impacto positivo nos resultados financeiros e na satisfação do cliente. A compreensão e a implementação eficaz da calibração de equipamentos de medição farão a diferença competitiva em um mercado cada vez mais desafiador.