10 Dicas Essenciais: Manutenção Preventiva e Calibração
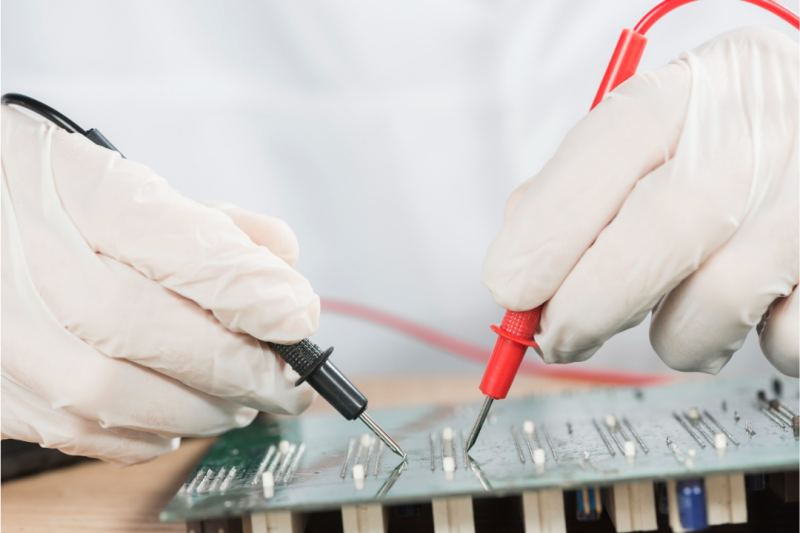
Por: Mauricio - 04 de Outubro de 2024
A manutenção preventiva e calibração de equipamentos são essenciais para garantir o funcionamento adequado e preciso de qualquer maquinário. Nesta postagem, exploraremos a importância dessas práticas, além de oferecer dicas para realizar calibrações eficazes, evitando erros comuns. Continue lendo para descobrir como essas ações podem prolongar a vida útil dos seus equipamentos e mantê-los sempre em excelência operacional.
Importância da Manutenção Preventiva
Manutenção preventiva é uma prática essencial para manter a integridade e o desempenho de equipamentos. Este tipo de manutenção é realizado regularmente para evitar falhas e prolongar a vida útil dos maquinários. Além de prevenir quebras inesperadas, ela garante que as máquinas operem de maneira eficiente, ajudando a evitar paradas não planejadas e perda de produtividade.
Em muitos setores, como o industrial e o médico, a precisão é primordial. A calibração dos equipamentos, incluindo a calibração de torquimetro de estalo, assegura que as medições sejam exatas e que a qualidade dos produtos e serviços seja mantida. Uma máquina bem calibrada evita a cadeia de erros que pode resultar em produtos defeituosos.
A manutenção preventiva inclui uma série de atividades, como inspeções regulares, limpeza, ajustes e substituição de peças desgastadas. O foco está em mitigar pequenos problemas antes que eles evoluam para questões maiores e mais custosas. Essa prática reduz a necessidade de reparos caros e diminui o tempo de inatividade dos equipamentos, o que repercute na eficiência operacional da empresa.
A importância de estabelecer um cronograma de manutenção preventiva consistente não pode ser subestimada. Identificar o momento certo para cada inspeção ou serviço é crucial para não comprometer o funcionamento das máquinas. Além disso, uma abordagem proativa ajuda as empresas a se prepararem melhor para o futuro, alocando tempo e recursos adequados quando antecipando necessidades de manutenção.
É importante lembrar que a manutenção vai além de simples correção de falhas. Durante as atividades preventivas, é possível detectar o desgaste de componentes, o que pode evitar acidentes e aumentar a segurança do ambiente de trabalho. Constantemente, problemas de segurança surgem de equipamentos que não foram adequadamente mantidos. A manutenção preventiva garante que os padrões regulamentares sejam cumpridos, evitando penalidades legais e possíveis danos à reputação da empresa.
Empresas que implementam estratégias de manutenção preventiva eficazes estão em uma posição melhor para otimizar seus recursos e enfrentar desafios. Elas fortalecem sua posição competitiva ao propiciar a continuidade operacional de forma mais eficaz e com custos controlados. Isso resulta, frequentemente, em uma vantagem de mercado, pois a confiabilidade dos equipamentos está diretamente ligada à satisfação do cliente e à retenção de clientes.
Uma das maneiras mais eficazes de implementar manutenção preventiva é através de sistemas de gestão e software que ajudam a monitorar e programar as atividades necessárias. Estas ferramentas permitem o registro de dados históricos e a análise de tendências, fornecendo informações valiosas que apoiam as decisões estratégicas sobre o gerenciamento de ativos.
Finalmente, a manutenção preventiva é especialmente valiosa para empresas empenhadas em políticas de responsabilidade ambiental. Manter equipamentos em boa condição reduz o consumo de energia e minimiza a geração de resíduos, contribuindo para práticas mais sustentáveis e reduzindo a pegada ecológica da organização.
Benefícios da Calibração Regular
A calibração regular de equipamentos oferece múltiplos benefícios que impactam diretamente a eficiência e a qualidade das operações em qualquer setor. O processo de calibração envolve ajustes finos para garantir que os instrumentos de medição forneçam valores precisos e confiáveis, mantendo a integridade na produção e nos serviços prestados.
Um dos principais benefícios da calibração é a precisão aprimorada. Ferramentas calibradas regularmente mantêm seus padrões de medição, o que é crucial em setores que exigem elevada precisão. Equipamentos fora de calibração podem gerar medições imprecisas, levando a falhas na qualidade dos produtos e na satisfação do cliente. Por isso, a calibração de esquadro é vital para assegurar exatidão em medidas críticas.
A calibração regular também ajuda a identificar problemas potenciais antes que afetem o funcionamento do equipamento. Ao detectar discrepâncias na medição, a empresa pode realizar ajustes necessários, evitando falhas significativas e custos inesperados. Esse monitoramento contínuo e proativo ajuda a prolongar a vida útil dos equipamentos, reduzindo a necessidade de substituir rapidamente peças ou dispositivos inteiros.
Além disso, a calibração periódica está alinhada com normativas e regulações industriais, garantindo que a organização esteja em conformidade com padrões nacionais ou internacionais. Isso não só evita sanções legais, mas também promove a confiança em clientes e parceiros de negócios que podem contar com a qualidade e a integridade dos produtos e serviços oferecidos.
Aumentar a eficiência operacional é outro benefício-chave. Equipamentos em bom estado de calibração oferecem resultados consistentes, permitindo que as operações prossigam sem interrupções ou retrabalho. Isto também contribui para esforços sustentáveis, já que operações eficientes tendem a consumir menos energia e minimizar o desperdício de materiais, alinhando-se a práticas empresariais ambientalmente conscientes.
Em muitas indústrias, como a farmacêutica e a aeroespacial, a calibração é vital para garantir a segurança. Qualquer desvio nos resultados pode ter consequências severas, tornando a calibração um elemento essencial para manter a segurança dos produtos e serviços finais. Isso inclui assegurar que o ambiente de trabalho e os produtos de consumo sigam rigorosos controles de qualidade.
Ademais, o processo de calibração regular fortalece a confiança interna na organização. Funciona como uma declaração de compromisso para com a alta qualidade e a busca por melhoria contínua. Os colaboradores, cientes de que as ferramentas estão ajustadas corretamente, podem focar mais em suas tarefas estratégicas e menos na preocupação com possíveis imprecisões de equipamento.
Por fim, integrar a calibração regular como parte dos processos de Manutenção preventiva e calibração de equipamentos contribui significativamente para a implementação de novas tecnologias e inovação. Equipamentos corretamente calibrados facilitam o teste e a implementação de novas soluções, garantindo que os resultados desses experimentos sejam fiáveis e replicáveis.
Em resumo, a calibração regular é uma prática indispensável que promove precisão, conformidade, eficiência, segurança e inovação. Esses benefícios não só impulsionam a confiabilidade e qualidade dos equipamentos, mas também impactam positivamente na reputação e sucesso da organização no mercado competitivo atual.
Passos para Calibrar Equipamentos
Calibrar equipamentos é uma tarefa crítica que garante a precisão e a confiabilidade dos instrumentos de medição. Independentemente do setor em que atuamos, seguir um procedimento padronizado é essencial para assegurar a integridade do processo de calibração. Abaixo, descrevemos os passos fundamentais para calibrar equipamentos de forma eficaz.
Primeiramente, é vital entender a documentação técnica do equipamento. A maioria dos equipamentos possui um manual que fornece orientações específicas sobre a calibração. Consultar este documento garante que os procedimentos recomendados pelo fabricante sejam seguidos, evitando danos ao equipamento ou falhas nos resultados de calibração.
O segundo passo é preparar o equipamento para calibração. Isso inclui a limpeza da unidade e a inspeção visual para identificar quaisquer sinais de desgaste ou dano físico que possam comprometer as medições. Além de preparar o equipamento, é essencial garantir que o ambiente esteja livre de interferências que possam afetar os resultados, como campos eletromagnéticos, vibrações ou condições extremas de temperatura.
Em seguida, certifique-se de ter os padrões de referência corretos. Esses padrões devem ser mais precisos do que o equipamento que está sendo calibrado. A escolha acertada dos padrões é crucial para garantir medições precisas. Em muitos casos, possuir padrões que são rastreáveis a entidades reconhecidas pelo governo ou autoridades internacionais é fundamental para validar o processo de calibração.
Uma parte crítica do processo envolve a execução da calibração em si. Use os padrões de referência para ajustar o equipamento conforme necessário, assegurando-se de que ele esteja medindo dentro dos limites especificados. Por exemplo, a Manutenção preventiva e calibração de equipamentos seguem métodos específicos para ajustes baseados em métricas obtidas durante verificações preliminares.
Após fazer os ajustes necessários, é importante registrar todos os dados obtidos durante o processo de calibração. Estes registros servem como documentação de que a calibração foi realizada corretamente e podem ser usados em auditorias para demonstrar conformidade com normas industriais. Manter um histórico de calibração é também valioso para prever quando futuras calibrações serão necessárias.
Após a calibração, realize uma verificação final para confirmar que os ajustes realizados colocaram o dispositivo dentro das especificações aceitáveis. Essa revisão final ajuda a garantir que o equipamento está operando de maneira ideal e capaz de fornecer medições precisas em aplicações futuras.
Finalmente, considere a frequência da calibração. Dependendo do tipo de equipamento e do seu uso, a frequência pode variar. É comum estabelecer um cronograma baseado em fatores como a taxa de utilização do equipamento, as condições do ambiente de operação e os requisitos regulatórios. Seguir um cronograma de calibração regular é essencial para manter a funcionalidade e a vida útil dos instrumentos.
Em resumo, a calibração é um processo que exige atenção aos detalhes e um planejamento cuidadoso. Um procedimento bem executado aumenta significativamente a confiança nas medições obtidas, melhora a produtividade e garante a qualidade do produto final. Além disso, adotar práticas consistentes de calibração fortalece a posição da empresa em seu compromisso com a excelência e a inovação.
Certificar-se de que todos os colaboradores estão treinados adequadamente nas práticas de calibração e que têm acesso às ferramentas e recursos necessários é também parte da execução bem-sucedida destes procedimentos críticos na operação.
Erros Comuns a Evitar na Manutenção
Embora a manutenção preventiva ofereça grandes benefícios para a durabilidade e funcionalidade dos equipamentos, existem erros comuns que podem comprometer todo o processo. Identificar e evitar esses erros é essencial para garantir que os equipamentos operem com precisão e eficiência ao longo do tempo.
Um dos erros mais frequentes é negligenciar o cronograma de manutenção. Muitos optam por adiar tarefas de manutenção devido a prazos apertados ou para evitar custos de inatividade, mas isso frequentemente leva a falhas mais graves e caras. Estabelecer e seguir um cronograma rigoroso de manutenção ajuda a mitigar essas situações, garantindo que os equipamentos sejam inspecionados e calibrados no tempo certo.
Outro erro comum é a falta de treinamento adequado dos funcionários. Sem o conhecimento e habilidades apropriados, é difícil realizar procedimentos de manutenção corretamente. Investir em formação contínua para o pessoal não só garante a execução correta das tarefas, mas também melhora a segurança no local de trabalho e aumenta a competência organizacional.
Usar peças ou materiais inadequados durante a manutenção é outro equívoco crítico. Reparos improvisados ou a escolha de peças de baixa qualidade podem causar danos a longo prazo ao equipamento. É fundamental sempre usar componentes respeitando as especificações do fabricante para alcançar o melhor desempenho e longevidade.
A falta de documentação é um erro comum que pode ter impactos adversos. Sem registros adequados dos serviços de manutenção realizados, é difícil acompanhar as condições do equipamento e prever futuras necessidades de manutenção. Registros completos e precisos ajudam a identificar tendências, planejar atividades de serviço e preparar para auditorias.
Um erro que muitas vezes passa despercebido é não considerar as condições ambientais que envolvem o equipamento. Fatores como temperatura, umidade e poeira podem afetar significativamente o funcionamento dos equipamentos. Avaliar e otimizar o ambiente de operação pode prevenir o desgaste prematuro e manter a eficiência dos dispositivos.
Superestimar a capacidade do equipamento também pode ser problemático. Forçar um maquinário além de suas capacidades projetadas pode resultar em falhas catastróficas. É crucial conhecer os limites de operação e respeitar as capacidades dos equipamentos para evitar danos dispendiosos.
Além disso, pular a fase de calibração ao realizar a manutenção é um erro que pode comprometer a precisão das operações. A calibração de instrumentos após a manutenção assegura que eles estão operando em níveis de precisão aceitáveis. Ignorar esse passo pode continuar a dar existência a erros de medição durante o ciclo de operação do equipamento.
Por fim, não revisar os métodos de manutenção pode levar ao uso de práticas desatualizadas que não maximizam a eficiência e a vida útil do equipamento. Revisar e atualizar regularmente os procedimentos garante que a organização esteja utilizando tecnologias e técnicas de ponta, minimizando riscos e melhorando a produtividade.
Compreender esses erros e tomar medidas para evitá-los é uma parte vital para garantir a eficácia da manutenção preventiva e calibração de equipamentos. Isso não só prolonga a vida dos equipamentos como também otimiza os recursos organizacionais e fomenta um ambiente de trabalho seguro e eficiente.
Após explorar os principais aspectos da manutenção preventiva e calibração de equipamentos, fica evidente a importância dessas práticas na otimização do funcionamento e prolongamento da vida útil dos maquinários. Seja compreendendo a importância da manutenção, reconhecendo os benefícios das calibrações regulares, ou aprendendo a evitar erros comuns, a relevância dessa abordagem não pode ser subestimada.
Convidamos você a aplicar essas práticas em seu ambiente de trabalho para garantir o máximo de eficiência e desempenho dos seus equipamentos. Compartilhe suas experiências ou dúvidas conosco; estamos ansiosos para ouvir sua opinião e continuar essa conversa enriquecedora.
E você, como pretende aplicar essas ideias no seu dia a dia? Pense nisso e comece a fazer a diferença hoje mesmo!